Precast Magnet Factory tells you how to choose high-quality precast shuttering magnet?
In the precast concrete industry, the precast shuttering magnet is a key piece of equipment widely used to fix steel side molds. Choosing a high-quality shuttering magnet can not only improve production efficiency but also ensure safety and stability during the production process. This article will discuss in detail how to choose high-quality precast shuttering magnets from aspects such as adsorption force, button coordination, shell bending, welding quality, etc., to help customers make wise decisions during the procurement process.
Adsorption is the primary indicator for selecting shuttering magnets
Definition and importance of adsorption force
Adsorption force refers to the magnetic force between the shuttering magnet and the steel side mold, which determines whether the shuttering magnet can firmly fix the side mold and is one of the most important indicators when selecting a shuttering magnet. The adsorption force of the shuttering magnet of precast concrete is directly related to the stability of the workpiece and the safety of construction. If the adsorption force is not strong enough, the shuttering magnet may lose its fixing effect during the production process, causing the side mold to loosen or shift, thereby affecting production quality and safety.
Standards and tolerances of adsorption force
Common shuttering magnets on the market generally claim that their adsorption force is 1000 kg (1 ton), however, the actual adsorption force may vary depending on the manufacturer's design, materials, and production process. Therefore, it is very important to understand the actual adsorption force standard of the shuttering magnet. For a 1-ton stainless steel shuttering magnet, the tolerance range of adsorption force should generally be within +/-50 kg. That is to say, in actual applications, the adsorption force of the shuttering magnet may fluctuate slightly, but the shuttering magnet within this range still meets the quality standards.
How to verify adsorption force
In order to ensure that the purchased shuttering magnet meets the adsorption force requirements, customers can verify the actual performance of the shuttering magnet through sampling inspection. First, the component factory can measure the adsorption force of the shuttering magnet through a vertical pull-out force test to ensure that it meets the design standards. In addition, large-scale products can be regularly inspected to ensure that the quality of the shuttering magnet is consistent. Before purchasing, customers should ask the supplier to provide relevant performance test reports to ensure that the adsorption force meets the requirements.
Risks and impacts of insufficient adsorption force
If the shuttering magnet has insufficient adsorption force, the following problems may occur:
· Side mold displacement: If the shuttering magnet has insufficient adsorption force, the steel side mold may move during the concrete pouring process, which may affect the production accuracy and the service life of the mold.
· Production safety hazards: Insufficient adsorption force of the shuttering magnet may cause the side mold to loosen, leading to accidents and endangering the safety of operators.
· Quality issues: If the shuttering magnet cannot firmly fix the side mold, the surface of the concrete product may be uneven or the shape may be irregular, thus affecting the quality of the final product.
Therefore, ensuring that the shuttering magnet has sufficient adsorption force is the key to preventing these problems.
Key coordination-the key to affecting ease of use
Key function and working principle
Shuttering magnets are usually equipped with keys to realize installation and removal functions. The function of the key is to control the connection and separation of the magnetic core in the shuttering magnet to ensure that the shuttering magnet can firmly fix the steel side mold. The key transmits the magnetic core to the top of the shuttering magnet through the connecting accessories to achieve locking and unlocking. The key design of the shuttering magnet directly affects its ease of use and work efficiency.
Importance of key coordination
Key coordination is crucial to the user experience of shuttering magnets. If the key is not flexible or smooth, the installation and removal of the shuttering magnet will become difficult, thus affecting production efficiency. Especially in a high-intensity working environment, operators need to frequently install and remove shuttering magnets, and the incoordination of keys may lead to reduced operator efficiency and even safety problems.
How to evaluate key coordination
When choosing a shuttering magnet, customers can evaluate the key coordination through actual operation. The flexibility of the key should be moderate, neither too loose nor too tight. In addition, the material of the key should have sufficient wear resistance to withstand long-term use. When purchasing, customers can ask the supplier to provide detailed instructions on the key design and function to ensure that the key can still maintain good coordination during long-term use.
Bending of the shell-design points to avoid shell damage
The role and design of the shell
The shell is the outer protective layer of the shuttering magnet, which mainly plays the role of protecting the internal magnetic core from external force impact. The design of the shell should have a certain strength and tensile resistance to prevent bending or collapse during use. High-quality shuttering magnet shells are usually made of stainless steel and are professionally welded and processed to ensure that they are durable enough.
Shell strength requirements
The strength of the shuttering magnet shell is directly related to the overall durability of the shuttering magnet. A high-strength shell can effectively prevent the shuttering magnet from being deformed or damaged during use, thereby ensuring the long-term stability of the shuttering magnet. In order to improve the tensile strength of the shell, a welding step is usually added inside the shell to prevent the shell from being deformed under external force.
Test the strength of the shell
When purchasing a shuttering magnet, customers can perform a simple test on the shell by using tools such as a crowbar. By repeatedly prying, it can be verified whether the shell bends or collapses when subjected to external force. If the shell cannot withstand a certain amount of pressure, it may affect the service life of the shuttering magnet. Therefore, customers should choose a shuttering magnet with a sturdy shell that is not easily deformed.
Shell welding firmness and uniqueness - ensuring the long-term stability of the shuttering magnet
The impact of welding quality on the stability of the shuttering magnet
Welding is a key process in manufacturing the shuttering magnet shell, which directly affects the stability and service life of the shuttering magnet. An unqualified welding process will lead to a loose connection of the shell, resulting in cracks, looseness, and other problems, affecting the normal use of the shuttering magnet. Therefore, customers should pay special attention to the quality of the welding process when choosing a shuttering magnet.
How to evaluate the welding quality of the shell
Customers can evaluate the welding quality by checking the welding parts of the shuttering magnet shell. High-quality welding parts should be smooth and uniform, and should not have obvious welding defects such as pores and cracks. In addition, customers can also ask suppliers to provide welding quality inspection reports to ensure that the product meets quality standards.
How to ensure the uniqueness and long-term use of the shell
In order to improve the long-term stability and durability of the shuttering magnet, manufacturers usually optimize the shell design to enhance its carrying capacity. When choosing, customers should understand the advantages and characteristics of different shell designs to ensure that the selected shuttering magnet can maintain efficient and stable performance during long-term use.
Other important standards and selection tips for high-quality shuttering magnets
Material selection and durability
The material of the shuttering magnet directly affects its durability and corrosion resistance. High-quality stainless steel can effectively improve the durability of the shuttering magnet and prevent corrosion and damage. Customers should give priority to stainless steel when choosing shuttering magnets, and avoid using low-quality or easily corrosive materials.
Production process and quality control
High-quality shuttering magnets need to undergo strict production process control, from the selection of raw materials to the inspection of the final product, each link needs to ensure that it meets the quality standards. Customers should choose suppliers with a complete quality control system to ensure that the purchased shuttering magnets have stable quality.
Brand and supplier selection
Brand and supplier selection is crucial to ensure product quality. Customers should choose shutter magnet manufacturers with a good reputation and rich experience to ensure that product quality is guaranteed. In addition, the supplier's after-sales service and technical support are also very important, and customers should ensure that they can obtain timely and effective technical support and product maintenance services.
When choosing a precast shuttering magnet supplier, HULK Metal stands out for its excellent quality, rich experience, and strong technical support. As a leading precast concrete shuttering magnet manufacturer in the industry, HULK Metal is committed to providing customers with high-quality, durable, and cost-effective shuttering magnet solutions. Our shuttering magnet products strictly follow international standards and have passed ISO 9001 certification to ensure that every product meets strict quality control requirements.
HULK Metal uses advanced production equipment and processes. All shuttering magnets are made of high-strength stainless steel materials, which are precision welded and heat-treated to ensure their excellent tensile strength and long-term durability. We also provide a full range of technical support and customization services and can design and produce according to the specific needs of customers to meet the specific requirements of different engineering projects. In addition, insert magnet and Magnetic Recess Former are also available.
Choosing a high-quality precast shuttering magnet is the key to ensuring the smooth progress of the precast concrete production process. By paying attention to the requirements of adsorption force, button coordination, shell strength, welding quality, etc., customers can choose the shuttering magnet that suits their needs. Regular inspection and maintenance of the shuttering magnet will greatly improve its service life and production efficiency, bringing higher production quality and safety guarantees to the precast concrete industry.
Article Navigation
PRECAST CONCRETE ACCESSORIES
OTHER RELATED ARTICLE
Other Precast Concrete Accessories You Might Want to Know
You can click to learn more about HULK Metal precast concrete accessories such as lifting anchors, precast sockets, spread anchors, shuttering magnets, cast-in channels, wire loop boxes, and other precast concrete accessories you might want to know.
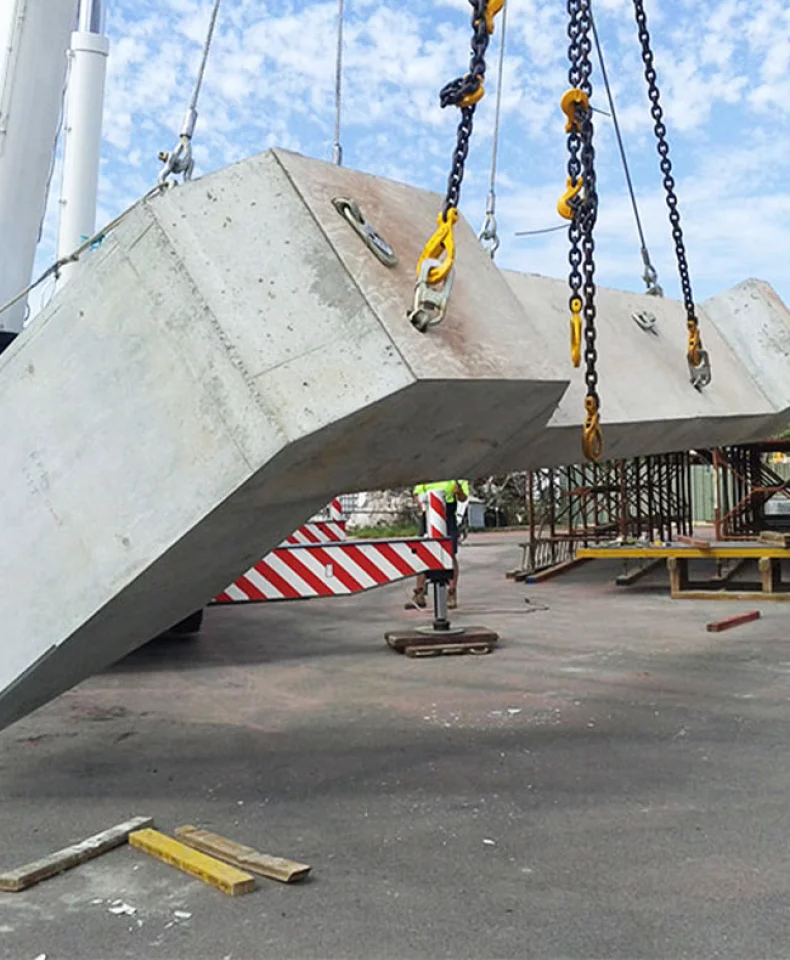