Comprehensive introduction to galvanizing
Overview
Definition:
Galvanizing is a surface treatment technology that covers the surface of metal, alloy or other materials with a layer of zinc to achieve corrosion protection and improve aesthetics. This process is widely used in industry, construction and consumer products. Its superior protective performance and low cost make it an indispensable processing method.
Historical background:
The history of galvanizing technology can be traced back to the 18th century when French scientists first discovered that zinc has anti-corrosion properties and proposed the concept of using it to protect metals. In the mid-19th century, hot-dip galvanizing was gradually industrialized, especially in the steel industry, where hot-dip galvanizing quickly became the mainstream technology for corrosion protection. In recent years, with the improvement of environmental protection requirements and the continuous research and development of new technologies, the galvanizing process has made significant progress in green production and performance optimization.
The main types of galvanizing
Hot-dip galvanizing:
·Process flow: Hot-dip galvanizing forms a zinc protective film by immersing the metal substrate in molten zinc liquid. The entire process includes surface cleaning, plating agent treatment, zinc immersion, and post-treatment. The zinc layer forms a metallurgical bond with the substrate and has extremely strong adhesion.
·Advantages and Disadvantages: The main advantages of hot-dip galvanizing are strong durability, excellent protection, and long-term use in harsh environments. However, due to the complex process, the surface finish of hot-dip galvanizing may not be as good as other methods.
·Scope of application: Hot-dip galvanizing is often used in fields that require high-strength protection, such as bridges, building steel structures, and traffic guardrails.
Cold galvanizing (electro galvanizing):
·Process flow: Cold galvanizing uses an electrochemical method to deposit zinc ions on the metal surface through electrolysis. The process steps include cleaning, activation, electroplating, and passivation.
·Advantages and Disadvantages: Cold galvanizing has a smooth surface and strong decorative properties, which is suitable for precision parts, but its zinc layer is thinner and its corrosion resistance is lower than that of hot-dip galvanizing.
·Scope of application: Widely used in home appliance housings, light equipment, and decorative parts.
Other galvanizing methods:
·Mechanical galvanizing: The coating is formed by the mechanical friction between zinc powder and metal parts, which is suitable for small parts.
·Spraying zinc: The zinc liquid is sprayed onto the metal surface through high-temperature spraying equipment, which is suitable for large components or local repairs.
·Application areas: These methods are mainly used in special scenarios, such as repairs, local coating, or special design requirements.
Thickness and performance of the galvanized layer
Standard thickness requirements: The thickness of the galvanized layer is usually determined according to the requirements of the use environment. For precast concrete accessories, the conventional thickness is more than 3 microns, and special demand scenarios may require higher requirements.
The impact of thickness on performance: The thicker the galvanized layer, the better its anti-corrosion performance, but an overly thick zinc layer may lead to a decrease in processing performance and increase costs. Therefore, scientific thickness selection is crucial.
Detection and control methods: Commonly used detection methods include magnetic thickness gauges, microscope slice analysis, and gravimetric detection. Through strict process control, ensure that the thickness of the galvanized layer meets the specification requirements.
Anti-corrosion principle of galvanizing
Physical barrier effect: The zinc layer forms a sealing barrier on the metal surface to isolate moisture and oxygen and prevent corrosion.
Electrochemical protection: The potential of zinc is relatively negative. When in contact with the iron substrate, zinc is preferentially oxidized, playing the role of a sacrificial anode to protect the substrate from corrosion.
Self-repairing ability of zinc layer: When the zinc layer is damaged, zinc salts will be formed to fill local damage, thereby providing continuous protection.
Advantages and limitations of galvanizing
Advantages:
· Cost-effectiveness: galvanizing is relatively inexpensive and has a long lifespan.
· Durability: Excellent protection in harsh environments.
· Low maintenance: The galvanized layer is wear-resistant and reduces maintenance frequency.
Limitations:
· Performance degrades in highly acidic or high-salt environments.
· Some precision machined parts may not be suitable for galvanizing.
Quality standards and testing of galvanized products
International and domestic standards: Commonly used galvanizing standards include ISO 1461, ASTM A123 and GB/T 13912. These standards have clear requirements for coating thickness, adhesion and uniformity.
Common testing methods:
· Coating thickness measurement: Use a magnetic or eddy current thickness gauge.
· Adhesion test: Evaluate the adhesion performance of the zinc layer through the cross-cut method or peel test.
Key points of quality control: Strictly monitor each link of pre-treatment, galvanizing, and post-treatment to ensure that product performance meets the standards.
Environmental and safety considerations
Environmental issues in the galvanizing process:
·Wastewater treatment: Zinc-containing wastewater needs to be treated by sedimentation and filtration.
·Waste gas emissions: Strictly control zinc fume and acid mist emissions to ensure compliance with environmental regulations.
Operational safety precautions:
·Prevent high-temperature burns and contact with electrolytes.
·Regularly maintain equipment to ensure safe operation.
Sustainable development direction:
·Develop chromium-free passivation technology.
·Promote low-energy galvanizing equipment.
Advantages of choosing HULK Metal as a supplier
Company profile: HULK Metal is a precast concrete accessories supplier with many years of experience, focusing on providing high-quality solutions to customers around the world.
Product quality assurance: The company is ISO 9001 certified, has professional testing equipment, and a strict quality control system to ensure that its products meet international standards.
Technical support and services: Our technical team provides customers with full-process support from design to production to ensure that the products meet specific needs.
Customer cases and word of mouth: HULK Metal's precast concrete accessories are widely used in multiple industries, and customer satisfaction continues to improve.
Diversified product lines: We offer a variety of galvanized products, including hot-dip galvanizing, cold-dip galvanizing, and other special coatings to meet the needs of different scenarios.
Importance of galvanizing technology: As an efficient anti-corrosion method, galvanizing has become one of the core technologies of modern industry.
The wide application and continuous development of galvanizing technology demonstrate its important position in modern industry. It is not only an efficient anti-corrosion method but also a key supporting technology for many industries to achieve sustainable development. From hot-dip galvanizing to cold-dip galvanizing, as well as various special processes, the diversity of galvanizing technology provides tailor-made solutions for different industries. With the enhancement of environmental awareness and the advancement of technology, the galvanizing process will continue to develop in the direction of greening and intelligence. Choosing HULK Metal as your partner means not only high-quality products but also professional technical support and excellent service experience. Let us work together to create a safer, more durable, and environmentally friendly future.
Article Navigation
PRECAST CONCRETE ACCESSORIES
Other Precast Concrete Accessories You Might Want to Know
You can click to learn more about HULK Metal precast concrete accessories such as lifting anchors, precast sockets, spread anchors, shuttering magnets, cast-in channels, wire loop boxes, and other precast concrete accessories you might want to know.
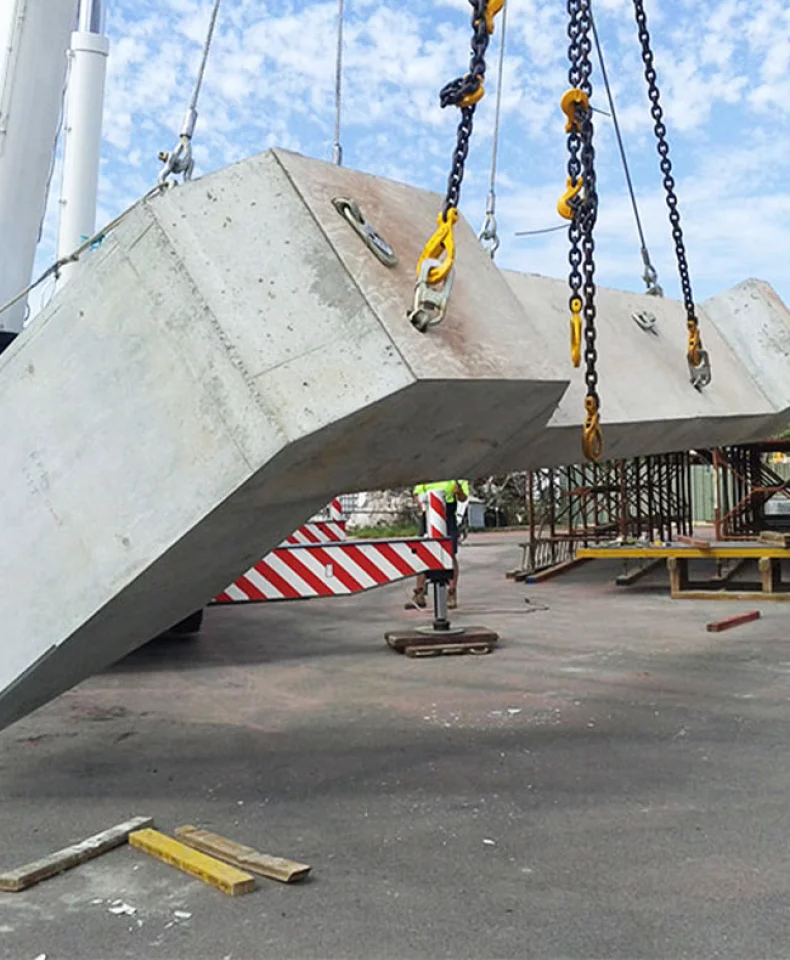