Precast magnet material--NdFeb
Common precast magnet materials and applications
The magnetic box is made of magnetic materials. Common materials include neodymium iron boron (NdFeB) magnets and permanent ferrite (Ferrite) magnets. These materials have excellent magnetic properties can generate strong magnetic fields, and are widely used in various fields of industry and daily life.
NdFeB permanent magnet material
NdFeB permanent magnet material is currently one of the strongest permanent magnet materials, and its core component is the intermetallic compound Nd2Fe14B. Compared with traditional cast aluminum nickel cobalt (Al-Ni-Co) permanent magnet materials and ferrite permanent magnet materials, NdFeB has a significantly higher magnetic energy product and coercive force, allowing it to generate more energy than its own volume. A stronger magnetic field. Specifically, the magnetic energy product and coercive force of NdFeB magnets far exceed those of ferrite materials, and they can absorb objects 640 times their own weight, showing extremely excellent magnetic performance.
NdFeB material has been widely used in modern industry, electronic technology, and medical fields due to its high energy density. It is widely used in miniaturized, lightweight, and thin equipment, such as instruments, electroacoustic motors, magnetic separation equipment, etc. In the medical industry, NdFeB magnets also play an important role, making medical devices and equipment more compact and efficient. Because of its excellent magnetic properties, NdFeB is known as the "Magnet King" and has been innovatively used in fields such as building fixed magnetic boxes.
Permanent ferrite material
Permanent magnet ferrite is a ceramic material with good magnetic properties. Its crystal structure is similar to natural magnetite (Pb(Fe7.5Mn3.5Al0.5Ti0.5)O19) and has a hexagonal crystal structure. Its chemical formula is MO·6Fe2O3 (where M is the divalent metal Pb, Ba, or Sr), so it is also called magnetoplumbite hexagonal ferrite or M-type ferrite. Ferrite magnets are generally cheaper than NdFeB magnets and have higher chemical stability and stronger high-temperature resistance, so they still have a place in some specific applications.
Permanent ferrite magnets are widely used in motors, speakers, sensors and other equipment, especially where corrosion resistance and high temperature resistance are required, their advantages are even more prominent. Although its magnetism is relatively weak, its stability and cost-effectiveness make it ideal for many industrial products.
Compare the two
When it comes to choosing the right magnet material, ferrite magnets and NdFeB magnets are two common choices, each with unique advantages and disadvantages. There are significant differences between the two in terms of appearance, magnetism, performance, and price. Here is a detailed comparative analysis of these two materials:
Appearance comparison
The appearance of ferrite magnets usually shows a rough texture, loose texture, and no obvious metallic luster. They are generally black or gray, so they are relatively low-key in appearance. Ferrite magnets are usually not electroplated because their surface is not easily oxidized, so their appearance does not require special protection.
NdFeB magnets have a silver-white metallic luster and a smooth surface. They are usually electroplated to prevent them from oxidizing in moisture or air and causing rust. NdFeB has a brighter appearance and stronger gloss, giving people a more refined and high-end impression.
Magnetic contrast
The magnetic force of ferrite magnets is generally mild, usually between 800-1000 Gauss, and the density is low, about 5 (g/cm³), which means that its magnetism is relatively weak and is suitable for applications with low magnetic requirements. occasion. Due to its relatively low magnetic force, ferrite is more used in low-frequency applications and equipment with general magnetic requirements.
In comparison, the magnetic force of NdFeB magnets is much stronger. In the bare magnetic state, the magnetic force of NdFeB can reach about 3500 Gauss, and the density is relatively high, about 7.5 (g/cm³). Because of its strong magnetic force, NdFeB is widely used in fields that require high magnetic force, such as motors, hard drives, audio systems, and other high-precision equipment.
Performance comparison
Ferrite magnets have significant advantages in temperature resistance and stability. Ferrite has a wide temperature range and can withstand higher temperatures without losing its magnetism, making it suitable for applications in high-temperature environments. The temperature resistance of NdFeB magnets is poor. The temperature resistance limit of ordinary NdFeB magnets is generally around 80°C. Once this temperature is exceeded, the magnetism will rapidly decrease or even be completely lost.
Although the magnetism of ferrite is weak, its high-temperature resistance and good stability make it more suitable in some special environments. NdFeB, on the other hand, has the advantages of stronger magnetism, small size, and lightweight, and is suitable for applications with higher magnetic requirements and smaller volume restrictions.
Price comparison
Ferrite magnets are relatively cheap, mainly because their raw materials are abundant and their processing is simple. The price of ferrite is usually calculated per piece, and the price will fluctuate depending on the shape, size and processing difficulty. Generally speaking, ferrite magnets are more economical and suitable for large-scale applications.
The price of NdFeB is more volatile and is usually priced according to the required grade and specific technical requirements. The price of NdFeB varies greatly with market supply and demand and may change daily due to market fluctuations. Therefore, the price of NdFeB is usually more expensive, especially in some high-end applications, where the cost will be higher.
Advantages and disadvantages of each
Advantages of ferrite magnets:
High magnetic permeability, low price, excellent high-temperature resistance, suitable for low-frequency magnetic field applications.
Stable performance, especially in environments with large temperature changes.
Disadvantages of ferrite magnets:
The magnetic force is weak and cannot meet the high magnetic demand, and the application range is relatively limited.
Advantages of NdFeB magnets:
Strong magnetic force, able to provide higher magnetic field strength in a small size.
Cost-effective, suitable for various applications requiring strong magnetic force, with good mechanical properties and long service life.
Disadvantages of NdFeB magnets:
Poor temperature characteristics and susceptibility to temperature changes, especially in high-temperature environments where performance drops significantly.
Fragile, especially prone to breakage when impacted by external forces, so care is required when using.
Specific applications
Wall fixed
In modern building construction, the installation efficiency of prefabricated walls directly affects the overall project progress. Using the HULK Metal magnetic precast fixing system, the accuracy and speed of the wall installation process can be greatly improved. Before installation, preset the magnetic box at the designated position on the mold table and start the magnetic system through the button lever. At this time, the magnetic force continuously attracts the prefabricated wall to firmly fix it on the formwork. Whether it is a large-scale construction project or a high-rise building that requires precise construction, HULK Metal magnetic boxes can effectively improve construction quality and ensure wall verticality and stability.
Compared with traditional fixing methods, this process eliminates the need for multiple manual adjustments and reinforcement steps, reducing the risk of manual operations and construction time. Moreover, magnetic adsorption makes the contact between the wall and the formwork table closer, avoiding installation errors caused by external vibration or wind. Therefore, this fixation method not only improves construction efficiency but also ensures that the prefabricated wall does not shift or tilt during the entire construction process and maintains a perfect geometric shape.
Floor installation
Floor installation is a key step in prefabricated construction. How to quickly and accurately install prefabricated floors in predetermined locations is related to the stability and safety of the entire building. The HULK Metal Magnetic Fixing System offers unique advantages in floor installation. The magnetic box is pre-embedded in the support structure under the floor. When the floor prefabricated parts are in place, the magnetic force will automatically attract and fix the floor. There is no need to use any nails or glue. The construction workers only need to place the floor prefabricated parts accurately into the designated position, and the magnetic force can quickly fix them firmly.
This application method simplifies the tedious work process in traditional floor installation and avoids long-term loosening, falling off, or deformation problems that may occur due to the use of nails, glue, and other fixing methods. In addition, because no traditional adhesive is used, this installation method avoids problems such as glue evaporation and air pollution, meets environmental protection requirements, and is suitable for construction projects with high environmental requirements, such as hospitals and schools.
House splicing
During the splicing process of houses, especially the installation of prefabricated roof components, precise docking is the key to ensuring structural stability and safety. The HULK Metal Magnetic System uses strong suction to enable adjacent roof prefabricated components to be quickly docked and firmly bonded, ensuring the integrity and stability of the overall structure. The high magnetic force of the magnetic box not only helps the components to be accurately aligned but also effectively resists the impact of external wind pressure, temperature changes, and other factors on the roof structure.
Especially in high-rise buildings or large industrial facilities, the splicing requirements of roof prefabricated components are higher and need to cope with complex environmental pressures. By using the HULK Metal magnetic fixing system, the installation of roof components is not only simple and efficient but also able to withstand harsh weather changes and maintain long-term stability and durability. Whether it is an area with high wind speed or an environment with large temperature fluctuations throughout the year, the magnetic system can effectively reduce interference from external factors and ensure that the roof structure does not loosen or shift.
The application of HULK Metal's magnetic prefabricated component fixing system in the construction industry can not only improve construction efficiency but also greatly improve installation accuracy and structural stability. Whether it is wall fixing, floor installation, or roof splicing, this system shows its unique advantages. It simplifies the construction process, saves a lot of manpower and material resources, reduces potential construction risks, and meets the requirements of modern architecture for high efficiency and environmental protection. As the construction industry continues to improve construction speed and quality, magnetic fixing systems have broad application prospects and will become one of indispensable technologies in the future construction industry.
Article Navigation
PRECAST CONCRETE ACCESSORIES
Other Precast Concrete Accessories You Might Want to Know
You can click to learn more about HULK Metal precast concrete accessories such as lifting anchors, precast sockets, spread anchors, shuttering magnets, cast-in channels, wire loop boxes, and other precast concrete accessories you might want to know.
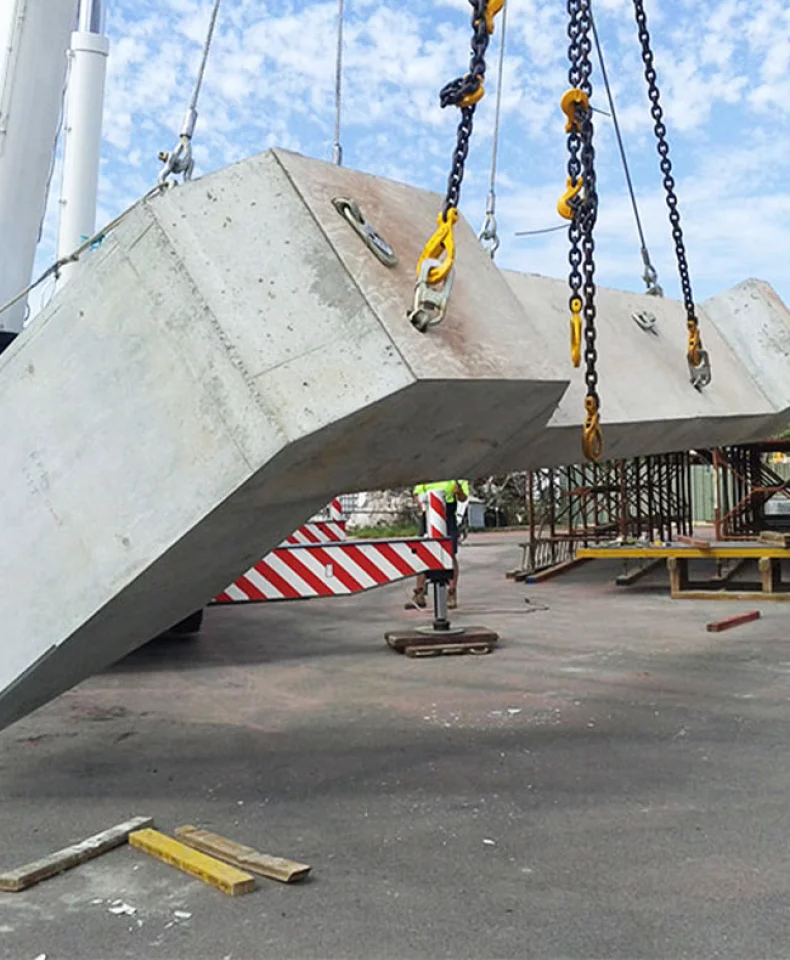