Surface treatment technology of precast concrete accessories
In modern construction projects, precast concrete accessories are not only basic components for connecting, supporting, and fixing structures, but also key elements to ensure the overall stability, safety, and durability of buildings. With the continuous development of construction technology, precast concrete accessories face more severe environmental challenges, such as humidity, corrosive chemicals, extreme climates, etc. In this context, surface treatment technology has become an important technical means to improve the performance of precast concrete accessories and extend their service life.
The necessity of surface treatment of precast concrete accessories
Improve corrosion resistance
precast concrete accessories are exposed to the external environment for a long time and are easily corroded by factors such as oxidation, moisture, salt spray, acid rain, etc., leading to corrosion, rust, and even structural failure. Through surface treatment processes such as galvanizing and spraying, a protective film can be formed on the metal surface, which significantly improves its corrosion resistance and delays material aging.
Enhance mechanical strength and wear resistance
Certain surface treatment processes (such as anodizing, heat treatment coating, etc.) can not only provide anti-corrosion protection, but also significantly improve the hardness and wear resistance of the metal surface, so that it can still maintain stable performance under high load, frequent friction, or impact conditions.
Improve appearance and aesthetics
Modern buildings also place higher demands on the appearance of accessories, especially on some exposed structural parts. Surface treatment can improve the surface finish and color consistency of the product, and even achieve decorative effects to meet the aesthetic needs of architectural design.
Extend service life
Untreated metal accessories are prone to corrosion or wear in a short period of time, shortening their service life. Surface treatment technology uses a multi-layer protection mechanism to extend the service life of accessories, reduce maintenance and replacement costs, and improve overall economic benefits.
Common surface treatment processes for precast concrete accessories
Hot-dip galvanizing
Hot-dip galvanizing is a process in which steel is immersed in molten zinc to form a zinc-iron alloy layer and a pure zinc layer. Its anti-corrosion principle mainly relies on the barrier effect of the zinc layer and the sacrificial anode effect.
·Process flow: degreasing → pickling → cleaning → plating → drying → immersion plating → cooling
·Advantages: strong anti-corrosion ability, uniform coating thickness, suitable for outdoor and marine environments
·Application scenarios: steel structure components, bridge connectors, highway guardrails, etc.
Electroplating
Electroplating is a process that uses the principle of electrolysis to deposit a metal layer on the metal surface. Common electroplated metals include zinc, nickel, chromium, etc.
·Process flow: pretreatment → electrolytic deposition → rinsing → drying
·Advantages: smooth surface, strong decorative effect, suitable for precision parts
·Limitations: corrosion resistance is not as good as hot-dip galvanizing, suitable for indoor use or mildly corrosive environments
Spraying and spraying (Powder Coating & Painting)
The spraying process is to spray powder coating or liquid coating evenly on the metal surface to form a protective film. Powder spraying is favored for its environmental protection and high adhesion.
·Process flow: surface treatment → electrostatic spraying → high temperature curing
·Advantages: rich colors, strong weather resistance, excellent UV resistance
·Applications: guardrails, exterior wall decorations, metal doors and windows, etc.
Phosphating
Phosphating is to form a layer of water-insoluble phosphate film on the metal surface to improve corrosion resistance and coating adhesion.
·Function: as an anti-rust base or pre-treatment for painting
·Advantages: low cost, mature process, suitable for mass production
·Common fields: automotive parts, building fasteners, etc.
Anodizing
Anodizing is an electrochemical treatment process for aluminum and its alloys, which improves corrosion resistance and hardness by forming a dense oxide film.
·Process flow: cleaning → anodizing → sealing treatment
·Advantages: high hardness, good corrosion resistance, coloring treatment
·Application: curtain wall aluminum profiles, decorative accessories, etc.
Sandblasting
Sandblasting is a process that uses high-speed sand flow to impact the surface to remove oxide layers, burrs, and impurities while improving coating adhesion.
·Function: surface cleaning and roughening treatment
·Advantage: improve surface roughness and enhance coating adhesion
·Often used in combination with other processes: such as spraying and pretreatment before galvanizing
Performance comparison analysis of different surface treatment processes
·Hot-dip galvanizing: suitable for heavy anti-corrosion scenarios, such as marine environments and outdoor facilities
·Electrogalvanizing: suitable for accessories with strong indoor decoration, with relatively low cost
·Powder spraying: both decorative and protective, suitable for modern architectural exterior parts
·Phosphating: often used as a base treatment to improve the adhesion of subsequent coatings
·Anodizing: the first choice for aluminum products, suitable for scenarios with high decorative requirements
Surface treatment process selection guide
Choose according to the use environment
·Outdoor/marine environment: hot-dip galvanizing or high-performance powder spraying is recommended, with excellent corrosion resistance.
·Indoor environment: electroplating or spraying can be selected, taking into account both decorative and economical properties.
·Chemical corrosion environment: consider phosphating + spraying or nano-coating combination process to enhance the protective effect
Choose according to the material of accessories
·Steel: hot-dip galvanizing, electroplating, spraying, etc. are all applicable.
·Aluminum alloy: Anodizing treatment has the best effect, combining beauty and corrosion resistance.
·Stainless steel: It can be electropolished and passivated to improve corrosion resistance.
Choose according to functional requirements
·High structural strength requirements: Choose processes that can improve hardness and wear resistance, such as anodizing or sandblasting + spraying.
·High appearance requirements: electroplating, spraying, and anodizing can provide a variety of colors and gloss effects.
Case analysis
·Large bridge projects: Use hot-dip galvanizing + anti-corrosion coating combination to ensure an anti-corrosion life of more than 50 years.
·Curtain wall aluminum profile project: Use anodizing + coloring process, which is both beautiful and weather-resistant.
·Underground pipe bracket: Spray after phosphating to adapt to humid environments and prevent rust.
HULK Metal's advantages in the field of surface treatment of precast concrete accessories
Advanced surface treatment equipment: HULK Metal has modern hot-dip galvanizing, electroplating, spraying, and anodizing production lines to ensure stable product quality.
Professional technical team: An experienced engineering team customizes the best surface treatment plan according to different project requirements.
Strict quality control system: Passed ISO 9001 certification, implemented full process quality management, and ensured that each batch of products meets international standards.
Global supply chain service: Relying on a strong logistics network, HULK Metal can quickly respond to global customer needs and provide efficient delivery solutions.
The surface treatment of precast concrete accessories is not only related to the appearance of the product but also directly affects its corrosion resistance, mechanical properties, and service life. Choosing the right surface treatment process can significantly improve the quality and economic benefits of construction projects. With advanced technology, rich experience, and excellent service, HULK Metal is committed to providing high-quality precast concrete accessories surface treatment solutions to global customers and is your trusted partner.
Article Navigation
PRECAST CONCRETE ACCESSORIES
Other Precast Concrete Accessories You Might Want to Know
You can click to learn more about HULK Metal precast concrete accessories such as lifting anchors, precast sockets, spread anchors, shuttering magnets, cast-in channels, wire loop boxes, and other precast concrete accessories you might want to know.
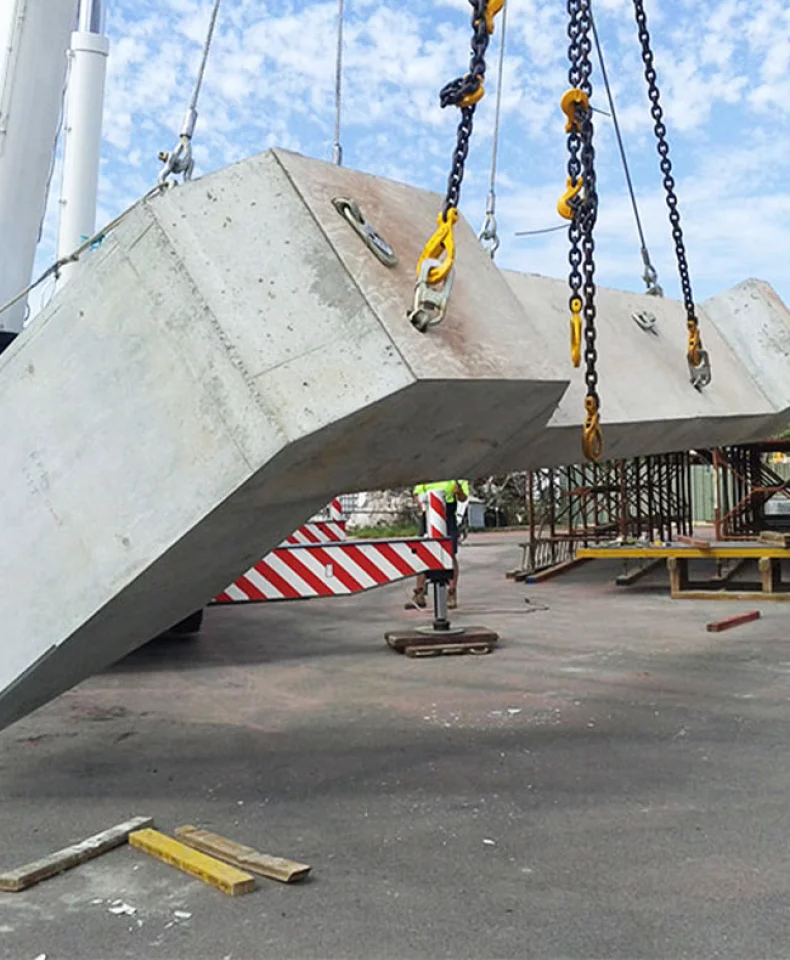