How to Choose High-Quality Shuttering Magnetic Products and Suppliers Guide
Magnetic Formwork System, also known as Magnetic Boxes, is an innovative technology in modern precast concrete component manufacturing and building formwork construction. The system is usually composed of high-performance NdFeB strong magnets and stainless steel housing, mainly including metal housing, a magnetic system, and an efficient on/off button. The core advantage of this design is its fast operation performance, which greatly improves the efficiency of formwork arrangement and removal. With the help of custom adapters, formwork magnets are used in the construction industry. Magnetic Formwork System is becoming an indispensable tool in reinforced concrete construction due to its high efficiency, precision, and safety. This system has a variety of applications in construction, which can significantly improve construction efficiency and reduce labor costs.
Application of Magnetic Formwork Systems in the Construction Industry
In the modern construction industry, it can be used for precise positioning, removal, and maintenance of steel bars.
For precise positioning of steel bars
The Magnetic Formwork System firmly fixes the formwork to the steel bars through strong magnets to ensure accurate positioning of the steel bars. This efficient positioning method can significantly reduce errors during construction and improve the quality of concrete pouring, thereby enhancing the overall safety and stability of the building structure.
Convenient removal and maintenance
Due to the unique design of the magnetic formwork system, removal work becomes more convenient and faster. Its magnetic adsorption characteristics make the formwork less likely to be damaged during removal, reducing waste and material loss at the construction site. At the same time, this system also provides a high degree of flexibility when the formwork needs to be changed or repaired, which helps to shorten the construction period.
Advantages of Magnetic Formwork System
Convenience:
The Magnetic Formwork System is very easy to use. Compared with traditional fixed molds, it uses magnetic fixing technology, which only requires gentle placement and adjustment to firmly fix the mold, without drilling or other mechanical fixing equipment, greatly simplifying the operation process and reducing the time of installation and removal. In addition, this system is compatible and can be integrated with various precast concrete molds and production lines, further improving its convenience.
Flexibility:
The design of the Magnetic Formwork System is very flexible and can adapt to different building components and complex architectural design requirements. Whether it is wall panels, floor slabs, beams and columns, the magnetic box system can be quickly adjusted to meet the specifications and shape requirements of different projects. Due to its strong magnetic properties, the mold configuration can be quickly changed without damaging the quality of the mold and concrete, making the production line more flexible and reducing downtime.
Efficiency:
The application of this system not only improves construction efficiency but also reduces production costs. Since traditional fasteners and bolts are no longer required, the use of magnetic boxes reduces labor costs and material waste. At the same time, the reusability and high durability of magnetic boxes ensure its long-term economic benefits. By reducing the time of mold disassembly and assembly and improving production accuracy, the Magnetic Formwork System greatly improves the production efficiency of prefabricated components and shortens the construction cycle, meeting the needs of building industrialization for efficient and high-quality production.
Working principle of magnetic formwork system
The core component of the magnetic formwork system is the magnetic array, whose structure is a special magnetic circuit design composed of high-performance NdFeB strong magnets and steel plates. The design provides extremely strong adsorption, which is mainly controlled by the size of the air gap. Therefore, the thickness and smoothness of the working surface directly affect the size of the magnet's adsorption.
Thickness of the working surface:
The thickness of the working surface determines the distance between the magnet and the adsorbed object. The smaller this distance, the stronger the magnetic field effect. Therefore, when selecting the working surface material of the template magnet, you should try to choose a material with moderate thickness to ensure the effectiveness of the magnetic suction.
Smoothness:
A smooth working surface can make the magnetic field more evenly distributed, thereby maximizing the suction. If the working surface is rough or uneven, the effective adsorption area of the magnet will be reduced, which will affect the adsorption effect. Therefore, when using the magnetic template system, you should ensure that the working surface is smooth and free of impurities.
The unique design of the magnetic template system enables fast and accurate positioning during construction. The template magnet activates the magnetic system by pressing the clamping handle to firmly adsorb the template to the specified position. When the template needs to be removed, use a professional crowbar to pry up the clamping handle. As the air gap between the magnetic array and the template increases, the adsorption force will be quickly released and the template can be quickly removed.
Instructions for use
To ensure the best performance of the magnetic template system, the following steps should be strictly followed during use:
Place the magnet:
Place the magnet of the magnetic template system in the specified position.
Activate the magnetic force:
Press the clamping handle, the magnetic system will activate the magnetic force, and the magnet will be firmly attached to the template or mold.
Release the magnetic force:
Use a professional crowbar to pry up the clamping handle. As the air gap between the magnetic array and the template increases, the suction will gradually release and the magnet will separate from the template.
Fixing accessories:
Using fixing screws, different types of side frames and reserved holes can be firmly fixed on the magnet to achieve a complex template structure design.
Proper use of the magnetic template system can not only improve construction efficiency, but also extend the service life of the equipment and reduce maintenance costs.
Maintenance of magnetic boxes
As an important part of the magnetic template system, the performance of the magnetic box directly affects the use effect and service life of the entire system. In order to ensure the normal operation of the magnetic box and extend its service life, the following maintenance measures should be taken:
Prevent damage and external force influence:
The magnetic box should be protected from strong impact and extrusion by external forces to prevent the magnet from being damaged or the shell from being deformed.
Keep the surface clean:
Similar to the magnetic lifter, the working surface of the magnetic box should be kept clean and smooth to avoid the adhesion of dust, iron filings, or concrete residues. These impurities will affect the adsorption force of the magnetic array and reduce work efficiency.
Ensure the flexibility of the clamping handle:
The clamping handle is a key operating component of the magnetic formwork system, and its flexibility will be affected by the intrusion of scrap iron and concrete. Clean and check the handle parts regularly to ensure its smooth operation.
Do a good job of rust prevention:
Although the shell of the magnetic box is usually made of stainless steel, in order to extend its service life, attention should still be paid to rust prevention. Clean it in time after use and use rust inhibitors for treatment when necessary.
Control the working temperature:
The working temperature of the magnetic box should be controlled below 80 degrees. Excessive temperature will reduce the magnetism of the NdFeB magnet and even cause magnetic failure, so special attention should be paid when using it in a high temperature environment.
How to choose shuttering magnets
HULK Metal, as a professional shuttering magnetic manufacturer, is well aware of the importance of choosing high-quality products. Here are some shopping guides to help you make smarter decisions when choosing magnetic fixing products.
Choose quality
Choose core
The core is the core of magnetic fixing products, and its performance depends directly on the quality of the magnet. High-quality magnets not only have strong suction, but their coating (anti-corrosion) and metal protective layer (anti-scratch) can also significantly extend the service life of the magnet. In order to ensure the working suction of the magnetic box, the suction test must be carried out by professional equipment before leaving the factory, as shown in the figure below. Simple testing equipment can monitor the working suction of the magnetic box after use at any time to detect the demagnetization situation and degree.
Choose shell
The shell of magnetic fixing products is generally made of high-strength carbon steel or stainless steel with a thickness of 3-4mm. High-strength carbon steel is better than stainless steel in strength, while stainless steel has an advantage in rust resistance. When choosing, the appropriate material and thickness should be determined in combination with the use environment. In addition, the frame structure design of the shell is also very important. The structure with reinforcing plate and latch design is more durable than direct welding.
Choose the model and quantity
After determining the supplier, choosing the appropriate model and quantity requires comprehensive consideration of the production process and usage scenario. For example, when producing laminated panels, it is recommended to use a magnetic box with a suction force of 600-800 kg and adjust the spacing according to the mold height and thickness. When producing on the assembly line vibration mold table, a 1000 kg magnetic box is more suitable; a 1350 kg magnetic box can be selected for the production of wall panels, and when producing prefabricated beams, columns, or other special-shaped components, it is recommended to use a 1800-2100 kg magnetic box with the corresponding clamp. Based on these data, the total amount of magnetic boxes and the budget required for the project can be accurately calculated.
Brand Selection
In today's rapidly developing prefabricated building market, how to select high-quality products from a large number of suppliers is the focus of every PC component manufacturer. In the absence of product trials, it is a wise choice to choose a supplier with brand influence. In addition, it is necessary to comprehensively consider the supplier's production equipment, production capacity, certification qualifications, quality control, and R&D capabilities, and combine the company's own development plan to make a final decision.
As an efficient tool in the production of prefabricated concrete components, the magnetic formwork system has the advantages of simple operation, quick installation, accurate positioning, and easy maintenance. Through proper use and regular maintenance, the system can significantly improve production efficiency, reduce construction costs, and improve the quality and safety of precast components. As a manufacturer of magnetic formwork systems, we are committed to providing customers with high-quality magnetic products and solutions to meet diverse construction needs. Whether in formwork layout, dismantling or special structural design, the magnetic formwork system brings higher flexibility and efficiency to the precast concrete industry.
Article Navigation
PRECAST CONCRETE ACCESSORIES
OTHER RELATED ARTICLE
- 1.Applications and advantages of swivel hoist rings: HULK Metal provides you with safer and more flexible lifting solutions
- 2.Understanding Load Capacity: A Guide to Lifting Anchor Strength
- 3.Lifting Clutch VS Lifting Ring Clutch:Definition, Working Principle, Application Scenarios, and Selection Guide
- 4.Concrete Screws:Which Type Should You Use?
Other Precast Concrete Accessories You Might Want to Know
You can click to learn more about HULK Metal precast concrete accessories such as lifting anchors, precast sockets, spread anchors, shuttering magnets, cast-in channels, wire loop boxes, and other precast concrete accessories you might want to know.
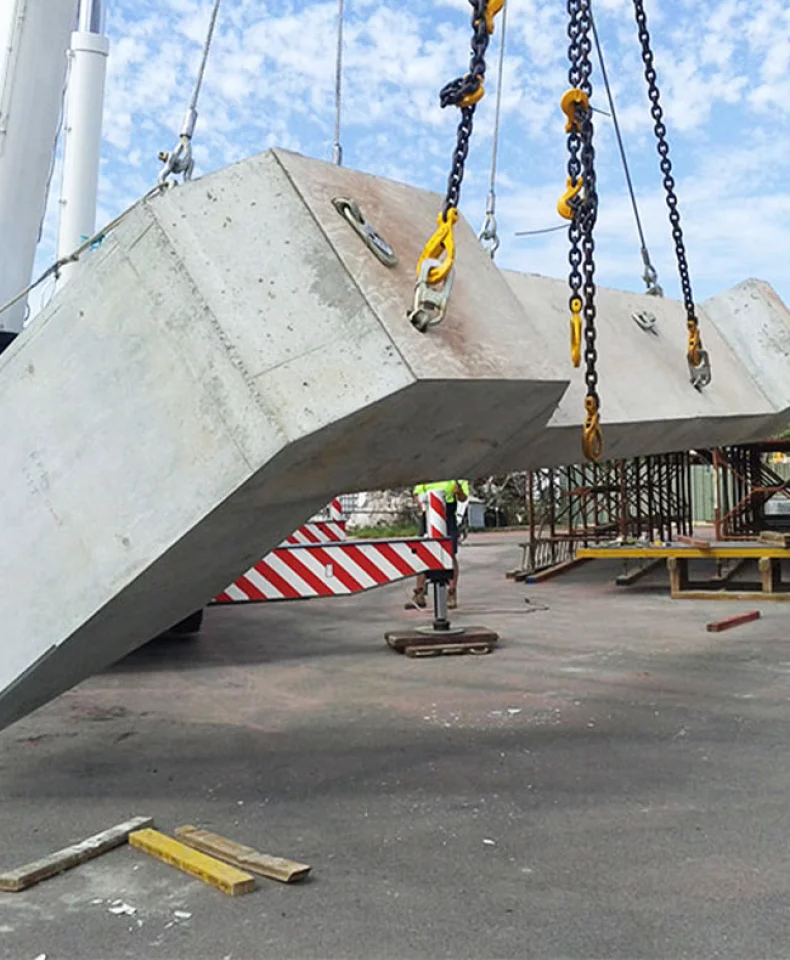