A 20-year-old factory tells you about application and manufacturing of precast concrete lifting clutch
Precast concrete lifting clutch, also known as dog bone lifting clutch, are integral components in the handling and positioning of heavy prefabricated elements. These devices are engineered to provide secure and efficient means of lifting, rotating, tilting, and maneuvering loads under various operational conditions. This article delves into the applications, materials, surface treatments, and quality assurance measures involved in the production of lifting clutches, ensuring they meet stringent safety and performance standards.
Applications of Precast Concrete Lifting Clutch
Lifting clutch are primarily utilized in construction and industrial settings where the handling of heavy prefabricated components is required. The design of the dog bone lifting clutch features a body with protruding lever arms and a high-strength lifting ring. The body includes a "T" shaped slot that engages with the head of the dog bone lifting anchor, enabling secure attachment. This design facilitates the lifting and maneuvering of loads, allowing for rotation and tilting as necessary. The lifting ring, composed of a shackle and clutch head, provides omnidirectional movement, ensuring flexibility in handling tasks.
The ability of the lifting clutch to rotate and tilt prefabricated elements under load is particularly beneficial in construction environments where precise positioning is crucial. For example, in the assembly of large concrete panels, lifting clutch enables workers to adjust the orientation of panels seamlessly, enhancing efficiency and safety on site.
Materials Used in Precast Concrete Lifting Clutch
The manufacturing of lifting clutch involves the use of high-grade materials to ensure durability and reliability under strenuous conditions. Key materials include:
Special Cast Head Clutch and Forged Bolt
Lifting clutch are manufactured using advanced materials such as 35CrMoV, a high-strength alloy steel known for its exceptional mechanical properties. This material is employed in the casting of the clutch head, which is subjected to high stress during lifting operations. Additionally, bolts used in the assembly are forged to enhance their strength and resistance to deformation.
Precision Casting and Forging
The components of lifting clutches undergo precision casting and forging processes. These methods ensure that each part meets stringent dimensional and performance criteria. Precision casting allows for the creation of complex shapes with high accuracy while forging improves the internal structure of the material, enhancing its mechanical properties and ensuring consistent quality.
Forged Alloy Steel Lifting Ring
The lifting ring, a critical component of the clutch, is made from forged alloy steel. This material is chosen for its superior tensile strength and toughness, which are essential for withstanding the dynamic loads encountered during lifting operations. The forging process also improves the grain structure of the steel, increasing its resistance to fatigue and wear.
Surface Treatment and Protection
To extend the lifespan of lifting clutches and ensure their performance in various environmental conditions, several surface treatment and protection methods are employed:
Hot-Dip Galvanizing
Hot-dip galvanizing involves coating the steel components with a layer of zinc, providing excellent corrosion resistance. This treatment is particularly effective in protecting the clutch from rust and deterioration, especially in outdoor or marine environments.
Electroplating
Electroplating is another method used to protect the surface of the lifting clutch. This process involves depositing a thin layer of metal, such as zinc or nickel, onto the surface of the component. Electroplating enhances corrosion resistance and can also improve the aesthetic appearance of the clutch.
Painting
For additional protection and to meet specific customer requirements, lifting clutches can be painted. Commonly used colors include yellow, which improves visibility and safety on construction sites. The paint provides a barrier against environmental factors and can be tailored to match company branding or operational needs.
Quality Assurance and Testing
Before lifting clutch are dispatched from the factory, they undergo rigorous testing and inspection to ensure they meet high safety and quality standards. The following tests are performed:
Visual Inspection
A thorough visual inspection is conducted to check for surface defects such as cracks, rust, deformation, and discoloration. This initial assessment helps identify any issues that could compromise the integrity of the lifting clutch.
Dimensional Inspection
Each component is measured to verify that it conforms to the specified dimensions. Accurate dimensions are crucial for ensuring proper fit and function when the clutch is used in lifting operations.
Load Testing
Lifting clutch are subjected to load testing at 1.5 times their rated capacity. This test verifies the clutch's ability to withstand the specified loads without failure. Load testing ensures that the clutches will perform reliably under actual working conditions, providing peace of mind to users regarding their safety and effectiveness.
The application of precast concrete lifting clutch in the handling of heavy prefabricated elements is indispensable in modern construction and industrial operations. Through the use of high-quality materials, precision manufacturing processes, and stringent quality control measures, lifting clutches are designed to provide reliable and safe performance. Whether it's rotating, tilting, or maneuvering heavy loads, lifting clutches offer the versatility and strength needed to meet the demanding requirements of today's construction and industrial projects.
Article Navigation
PRECAST CONCRETE ACCESSORIES
OTHER RELATED ARTICLE
Other Precast Concrete Accessories You Might Want to Know
You can click to learn more about HULK Metal precast concrete accessories such as lifting anchors, precast sockets, spread anchors, shuttering magnets, cast-in channels, wire loop boxes, and other precast concrete accessories you might want to know.
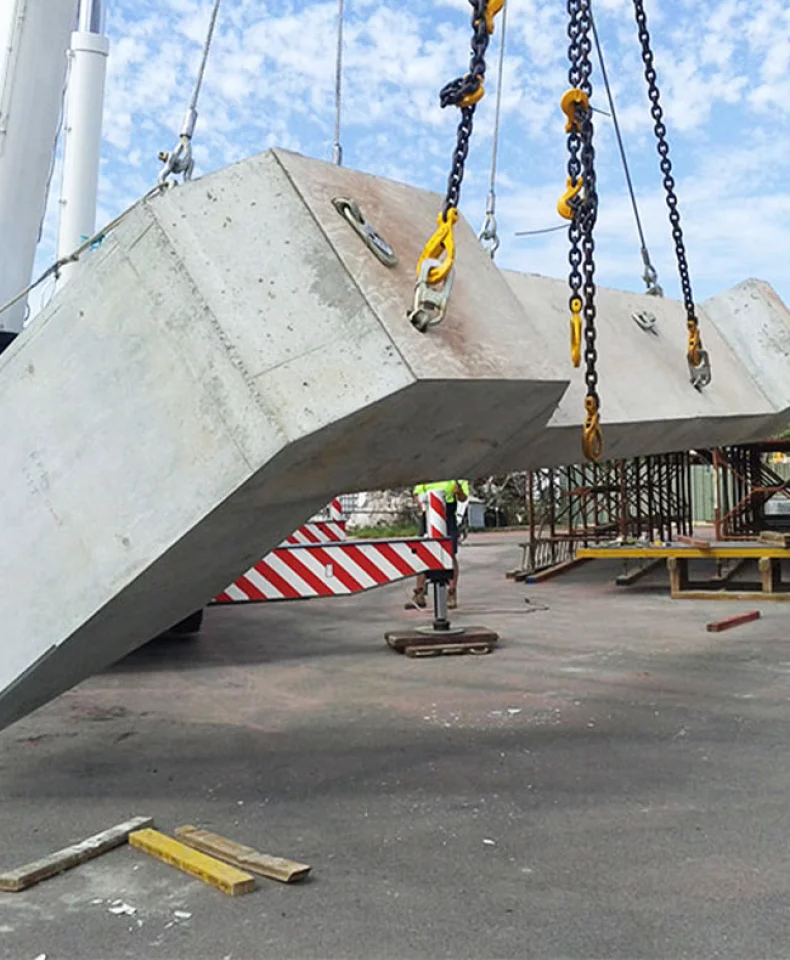