In-depth analysis of concrete screws: design, performance and application
As a key fixing part in modern building and engineering construction, concrete screws occupy an important position in the fixing scheme of the construction site due to their convenient installation, high load-bearing capacity, and wide applicability. They can not only cope with a variety of material substrates but also provide a fast and efficient installation method without complicated operation. This article will discuss in detail the design characteristics, material selection, performance advantages, practical applications, and market trends of concrete screws, providing a comprehensive reference for construction companies, engineers,and technicians.
Definition and working principle of concrete screws
Definition
Concrete screws are fasteners that are directly screwed into concrete, masonry, or other hard substrates. Unlike traditional expansion bolts, it uses the mechanical bite force between the thread and the substrate to achieve efficient fixation without the use of expansion sheets or chemical adhesives. The design of the screw enables it to be installed in a shorter time and causes less damage to the substrate when disassembled. This feature is particularly suitable for scenarios that require flexible adjustment or multiple disassembly and assembly.
Working principle
Mechanical bite
The thread of the screw forms a strong bite with the substrate by cutting or compacting the hole wall when screwing into the substrate.
Friction Enhancement
Serrated or high-low thread design provides a larger surface contact area, improving pull-out resistance.
Key Design and Material Analysis of Concrete Screws
Thread Shape and Structure
The threads of concrete screws are usually designed in the following two ways:
Serrated thread
It has excellent cutting force, which can reduce damage to the substrate and improve installation efficiency.
High-low thread
Through alternating thread height, the mechanical bite force with the hole wall is enhanced, which is suitable for high-intensity load scenarios.
In addition, the self-tapping design at the end of the screw helps to improve drilling accuracy while reducing the chance of jamming during installation.
Material and Surface Treatment
Material
Concrete screws are usually made of high-strength carbon steel, stainless steel, or alloy steel. Carbon steel has extremely high hardness and strength after heat treatment, while stainless steel is suitable for highly corrosive environments such as marine engineering and chemical facilities.
Surface Treatment
Galvanizing, electroplating, or coating with corrosion-resistant layers are common treatments to improve the corrosion resistance of screws and extend their service life. For extreme environments, nano-coating or special coating technologies are gradually being adopted.
Head design
Different head forms determine the applicable scenarios of concrete screws:
Hexagonal head
Easy to operate with a wrench, suitable for industrial equipment installation.
Countersunk head
common in furniture or decoration installation, ensuring aesthetics and concealment.
Round head
widely used in light fixing tasks, providing uniform force distribution.
Performance advantages of concrete screws
Efficient installation
Concrete screws do not require pre-installation of expansion sleeves or the use of chemical anchors. During construction, they only need to drill holes and screw in directly, which greatly improves installation efficiency. In addition, it reduces the need for construction tools and reduces overall costs.
Excellent pull-out resistance
The thread design ensures that the screws can withstand high pull-out and shear forces, and show stability and reliability regardless of static or dynamic loads. This feature is particularly critical in construction and heavy-duty equipment installation in seismic zones.
Removable and reusable
Concrete screws do not cause significant damage to the substrate when removed and can be reused. This flexibility makes it an ideal choice for engineering scenarios that require temporary fixation.
Adapt to a variety of substrates
Applicable to ordinary concrete, reinforced concrete, brick walls, and lightweight materials. It also shows excellent adaptability for connecting heterogeneous structures.
Application fields of concrete screws
The versatility of concrete screws makes it widely used in various types of construction and engineering. The following are its main application fields:
Construction engineering
It is used for fixing pipe supports, guardrails, and scaffolding of reinforced concrete structures and is especially suitable for fast construction needs.
Mechanical and electrical equipment installation
In the fixing of air conditioner outdoor units, solar brackets, and power equipment, concrete screws are favored for their convenient installation and stability.
Furniture and decoration
In residential and commercial decoration, concrete screws can provide concealed, beautiful, and durable fixing solutions, such as hanging paintings, chandeliers, and other installation tasks.
Industrial equipment and infrastructure
High-strength concrete screws are widely used in the fixing of heavy equipment, such as machine tool bases and conveyor belt brackets.
Marine and outdoor engineering
In the installation of coastal facilities, bridges, and outdoor facilities, stainless steel concrete screws ensure long-term use with their superior corrosion resistance.
Concrete screw selection and installation guide
Choosing the right concrete screw is the key to ensuring the fixing effect. The following is a detailed selection and installation guide:
Determine the load requirements
According to the load requirements of the specific scenario, calculate the required pull-out force and shear force, and select the appropriate screw length and diameter.
Substrate type matching
Select the corresponding thread type and material for different substrate densities and strengths to avoid fixation failure caused by substrate damage.
Drilling and cleaning
Before installation, use a matching drill bit to drill holes and clean the dust and debris in the holes to ensure seamless contact between the screw and the substrate.
Installation method
Use an electric impact wrench to apply force evenly to avoid tilting or over-tightening the screws to affect the fixing strength.
Quality Acceptance
After the installation is completed, perform a pull-out test to ensure that it meets the design load requirements, especially in high-strength scenarios.
Future development trends and technological innovations
As the construction industry's demand for efficient and safe construction increases, concrete screws continue to evolve in technology and the market:
Material innovation
The research and development of new high-strength alloy steels and lightweight materials will further improve the load capacity and durability of screws.
Intelligent installation equipment
The introduction of automated construction equipment will significantly improve construction efficiency and precision and meet the needs of large-scale projects.
Green Manufacturing
With the strengthening of environmental protection concepts, low-energy manufacturing processes and recyclable materials will become an important direction for the development of concrete screws.
Concrete screws have become a key solution in modern construction due to their convenient installation, efficient fixing, and adaptability to a variety of scenarios. Whether in the field of industry, construction, or decoration, it has demonstrated excellent performance and value. In the future, with the improvement of materials and process technology, the application potential of concrete screws will be broader, bringing more convenience and breakthroughs to the construction industry.
For more technical support or product consultation, please contact HULK Metal, we will wholeheartedly provide you with professional solutions and customized services.
Article Navigation
PRECAST CONCRETE ACCESSORIES
Other Precast Concrete Accessories You Might Want to Know
You can click to learn more about HULK Metal precast concrete accessories such as lifting anchors, precast sockets, spread anchors, shuttering magnets, cast-in channels, wire loop boxes, and other precast concrete accessories you might want to know.
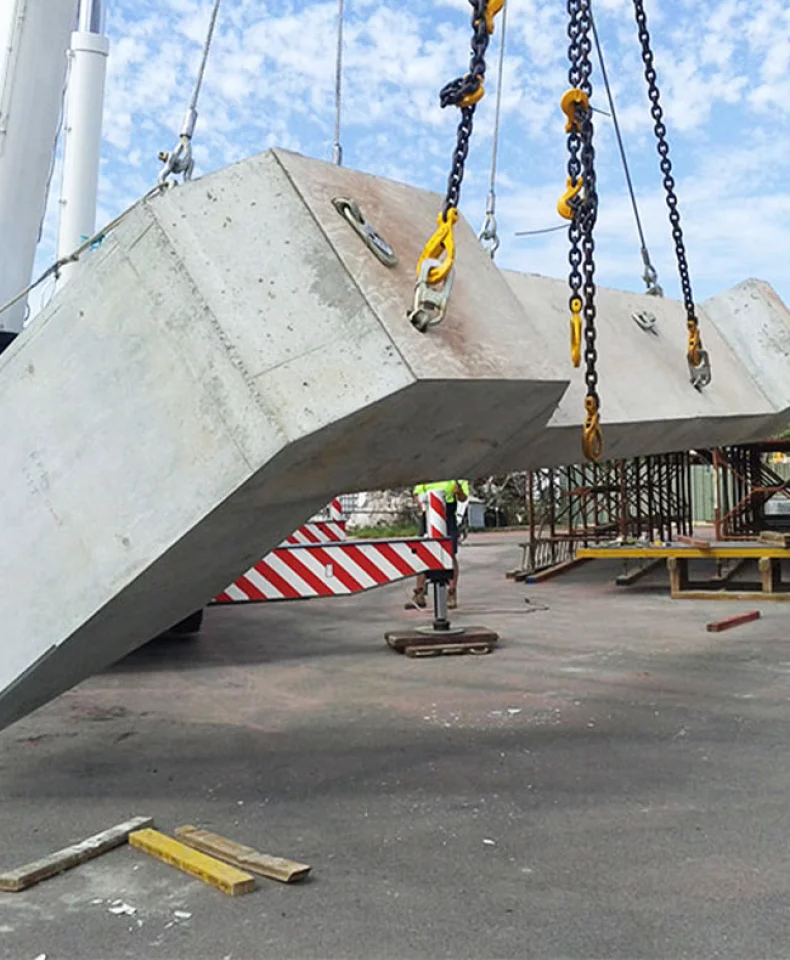