High-performance rubber recess formers: high-quality materials, precision manufacturing and strict quality control
Rubber Recess Former is a key auxiliary tool for precast concrete components. It is mainly used to form standardized grooves for installing lifting systems (such as lifting anchors) or other fasteners. In construction, infrastructure construction, rail transit, energy, and other industries, rubber recess formers are widely used due to their high precision, durability, and ease of use.
This article will comprehensively analyze the definition, materials, manufacturing process, application scenarios, installation steps, maintenance, and industry selection standards of rubber recess formers to help construction units, engineering contractors and purchasers better understand its functions and advantages.
What is a rubber recess former?
The role of rubber recess former
The main function of the rubber recess former is to form standardized grooves on the surface of concrete components to ensure that the lifting device can be installed smoothly. These grooves are usually used for:
·Connecting the lifting clutch (Lifting Anchor) to achieve safe and efficient lifting operations.
·Fix the anchor system to improve the bearing capacity of the concrete structure.
·Reserve space for pipelines or fixings to ensure accurate installation of equipment.
Main application scenarios
rubber recess formers play an important role in multiple industries, and common applications include:
·Construction industry: Standardized lifting points for prefabricated beams, plates, columns, and other components.
·Infrastructure: Lifting operations of concrete components such as bridges, subways, and highways.
·Power and energy: Lifting needs of transmission tower bases and wind power foundations.
·Port terminals: Used for the installation of large concrete pile foundations, offshore platforms, and other components.
·Rail transportation: Lifting solutions for prefabricated components of subways and high-speed railway bridges.
Materials and manufacturing processes of rubber recess formers
Selection of rubber materials
rubber recess formers generally use special rubber materials that are resistant to high temperatures, oil, and corrosion to ensure their stability in different construction environments. Common rubber materials include:
·Natural rubber (NR): has good elasticity and wear resistance, suitable for general construction environments.
·Synthetic rubber (SBR): has better oil resistance and anti-aging ability, suitable for long-term repeated use.
·Silicone Rubber: Excellent high-temperature resistance, suitable for extreme climate conditions.
·Polyurethane Rubber (PU): Stronger wear resistance, especially suitable for high-intensity construction scenes with frequent use.
Manufacturing process
rubber recess formers are usually produced by compression molding or injection molding:
Compression molding: The rubber raw material is heated to a certain temperature and placed in the mold, and high-pressure molding is used to ensure the product size is accurate and the surface is smooth.
Injection molding: The rubber is injected into the mold by high pressure, and then molded after high-temperature vulcanization, which improves production efficiency and enhances product durability.
Technical characteristics of rubber recess formers
High-temperature resistance
rubber recess formers can usually withstand construction temperatures of 80℃ to 120℃, while formers made of high-performance materials such as silicone rubber can withstand environments up to 250℃, making them suitable for high-temperature maintenance environments.
Oil resistance and corrosion resistance
During the construction process, the rubber recess former may come into contact with release agents, lubricants, chemical solvents, and other substances. The selection of high-performance rubber materials makes the former have excellent oil resistance and is not easy to age or deform, thus extending its service life.
Reuse
Compared with disposable plastic or metal formers, rubber recess formers can be reused many times and can be restored to use with simple cleaning, effectively reducing construction costs.
Accurately match lifting clutches of different sizes
Lifting Clutches with different load requirements requires grooves of different sizes. HULK Metal can provide customized rubber recess formers to ensure perfect matching of customer needs and improve construction accuracy.
Installation process of rubber recess former
Preliminary preparation
Ensure that the construction template is clean and free of dust and oil.
Ensure that the former is not damaged and check whether the rubber has cracks or aging.
Installation steps
Fix the former: Install the rubber recess former to the specified position of the concrete template. It can be fixed by magnetic fixers or mechanical clamps.
Pour concrete: Pour concrete according to construction standards to ensure that there are no bubbles or inclusions around the former to prevent affecting subsequent installation.
Wait for the concrete to solidify: usually 24-48 hours, depending on the ambient temperature and concrete mix.
Demoulding and removing the former: After the concrete has completely hardened, carefully remove the formwork and remove the rubber recess former to avoid damaging the groove shape.
Subsequent inspection: Make sure that the groove size and position meet the design requirements, and clean the former for next use.
Common problems and solutions
The former is not installed firmly, how to deal with it?
·Solution: Use a high-magnetic fixture or mechanical clamp to ensure that the former does not shift during the pouring process.
Are there bubbles or unevenness on the edge of the groove?
·Solution: When vibrating concrete, ensure that the vibration is uniform and use a high-flow concrete mix.
If the former is damaged or deformed, can it continue to be used?
·Solution: Check whether it is caused by overuse or improper storage. If obvious cracks or deformation are found, replace it with a new one to ensure construction quality.
Why choose HULK Metal's rubber recess former?
In the construction, infrastructure construction, and precast concrete industries, it is crucial to choose a reliable supplier of rubber recess formers. With rich industry experience, advanced production technology and a strict quality management system, HULK Metal provides high-quality rubber recess formers to customers around the world, ensuring that the products can maintain excellent performance in various construction environments.
Professional Manufacturer
HULK Metal has been deeply involved in the field of building embedded parts and lifting systems for many years. It has a complete R&D, production, testing, and supply chain management system, and can provide high-quality products that meet the needs of different projects. Our rubber recess formers adopt precision design and strict manufacturing standards to ensure accurate dimensions and easy installation and can be adapted to various concrete lifting and anchoring systems, helping customers improve construction efficiency and project quality. In addition, HULK Metal's professional team can provide technical support according to different application scenarios to ensure that the products achieve optimal performance in actual use.
High-quality rubber materials
The quality of rubber materials directly affects the durability and application range of the former. HULK Metal uses highly wear-resistant, high-temperature-resistant, and corrosion-resistant rubber materials to ensure that the products can still maintain stable performance in extreme construction environments. Whether in construction sites with high temperatures, high humidity, or chemicals, our rubber recess formers can provide excellent anti-aging and weathering resistance, effectively extending the service life. In addition, our products have good elasticity and impact resistance and can maintain good shape and function after repeated use, reducing losses during construction.
Customized solutions
HULK Metal is well aware that the needs of different customers are different, so it provides a full range of customized services to ensure that the rubber recess formers can be fully adapted to different lifting clutches and precast concrete components. We can adjust the size, hardness, wear resistance and special surface treatment of the former according to customer needs to improve the applicability and construction convenience of the product. HULK Metal's customized service not only ensures that the former is perfectly matched with various lifting systems, but also optimizes installation efficiency, reduces construction errors, and improves safety.
Strict quality control
Quality control is one of HULK Metal's core competitive strengths. All products are certified by the ISO 9001 quality management system and have passed international certifications such as CE and SGS to ensure that product quality meets global market standards. During the production process, we use advanced rubber processing technology and strict quality inspection procedures, including material testing, dimensional inspection, wear resistance testing, anti-aging testing, and load testing, to ensure that each product has high reliability and consistency. In addition, HULK Metal's quality inspection team will conduct a full range of inspections on each batch of products, from the entry of raw materials to the shipment of finished products, to ensure that every product delivered to customers meets the highest industry standards.
Choosing HULK Metal's rubber recess former not only means choosing products with high-quality materials, precision manufacturing, and strict quality control but also means having industry-leading technical support and customized solutions. Whether it is a large-scale construction project or a refined construction project, HULK Metal can provide efficient and reliable products and services to help global customers improve construction quality and efficiency.
Article Navigation
PRECAST CONCRETE ACCESSORIES
Other Precast Concrete Accessories You Might Want to Know
You can click to learn more about HULK Metal precast concrete accessories such as lifting anchors, precast sockets, spread anchors, shuttering magnets, cast-in channels, wire loop boxes, and other precast concrete accessories you might want to know.
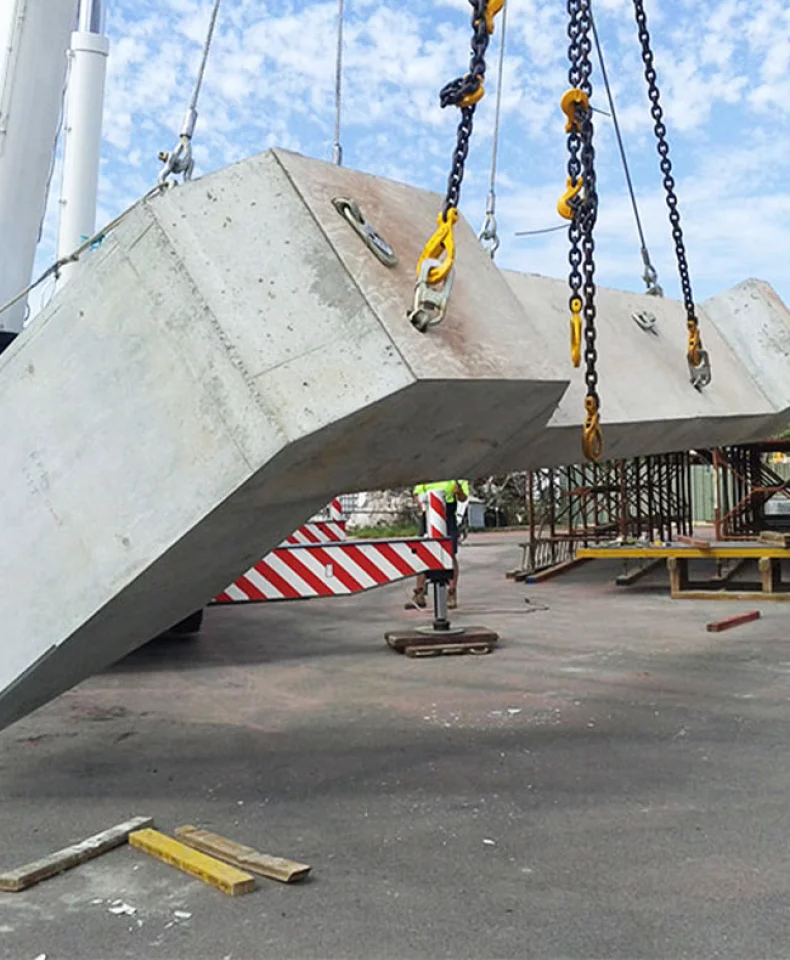