Safety Guide to Your Lifting Hooks
In today’s fast-paced industrial environment, ensuring safety during lifting operations is paramount. Whether you’re using cranes, hoists, or slings, the lifting hook is one of the most critical components in the rigging process. This comprehensive guide aims to help professionals and site managers select and use lifting hooks safely, understand the various types available, and adopt best practices that align with industry standards and Google’s preference for detailed, authoritative content.
Introduction
Lifting hooks play a crucial role in a wide range of industrial applications. They serve as the primary connection point between the load and the rigging system, making their safety and integrity essential for preventing accidents. This guide addresses the most important aspects of lifting hook safety—from choosing the right type of hook for your project to understanding how environmental factors can impact performance. By incorporating data-backed best practices and expert insights, we provide the necessary information to ensure that every lifting operation is conducted safely and efficiently.
Understanding Lifting Hooks
Lifting hooks are engineered components designed to handle heavy loads during lifting operations. Typically made from high-grade steel or other durable alloys, these hooks are available in various sizes and configurations to match specific load requirements. The material composition and manufacturing process are critical, as they determine the hook’s resistance to wear, corrosion, and mechanical stresses. Industries such as construction, manufacturing, and logistics rely heavily on lifting hooks to safely move equipment, structural elements, and other heavy loads.
The design of lifting hooks also reflects the need for precision engineering. A well-designed hook not only supports the load but also minimizes the risk of accidental disengagement, slippage, or damage to adjacent rigging components. Understanding the properties of different metals, such as tensile strength and resistance to extreme temperatures, is vital for ensuring that your selected hook will perform reliably under demanding conditions.
Types of Lifting Hooks
A wide variety of lifting hooks is available on the market, each tailored for specific applications. The following are some of the most widely used types in the rigging and lifting industry:
Eye Hooks
Eye hooks are characterized by their closed-loop design, which provides a secure attachment point for slings and chains. They are often used in scenarios where a stable, fixed connection is required. Eye hooks are particularly valued for their ability to distribute the load evenly across the hook, reducing the risk of deformation.
Clevis Hooks
Clevis hooks feature a U-shaped design with a pin for securing loads. This type is highly versatile and frequently used in conjunction with hook safety latches to ensure that the load remains securely attached. Their design makes them ideal for applications requiring quick engagement and disengagement without compromising safety.
Swivel Hooks
Swivel hooks are engineered with a rotating mechanism that allows the hook to adjust its position under load. This flexibility minimizes the risk of tangling or twisting in the rigging system, making them particularly useful in dynamic lifting operations where the load might shift or rotate.
Sorting Hooks
Sorting hooks are designed for specific applications where loads must be guided into precise positions. These hooks often incorporate specialized features that allow for controlled movement, ensuring that items are correctly sorted or positioned during the lifting process.
Foundry Hooks
Foundry hooks are heavy-duty components manufactured through casting processes. Known for their robustness, they are ideal for extremely high load capacities and harsh working environments. Their construction is particularly suited for applications in heavy industry where durability and strength are non-negotiable.
J-Hooks
K-hooks are shaped like the letter “J” and are used primarily for lifting operations that require a secure grip on irregular or challenging load shapes. Their design provides a natural locking mechanism that reduces the risk of accidental disengagement during lifting.
Grab Hooks
Grab hooks are designed with an integrated safety latch mechanism that prevents the hook from unintentionally releasing the load. They are commonly used in applications where safety is a top priority, especially in scenarios involving complex rigging systems or fluctuating load dynamics.
By categorizing these hooks, professionals can better match the type of hook to the specific demands of their project. The precise engineering behind each hook type ensures that even under challenging conditions, the rigging system remains secure and efficient.
The Role of Safety Latches
Safety latches are essential for preventing accidental disengagement during lifting operations. These devices secure the connection between the sling and the hook, ensuring that even if the load shifts or the rigging system experiences slack, the load remains firmly in place. While not all hooks are equipped with safety latches, many of the rigging hooks described above—such as grab hooks and clevis hooks—are routinely used with latches for added security.
It is important to regularly inspect safety latches for signs of wear or damage. A compromised latch can lead to load slippage, posing serious risks to personnel and equipment. Operators should follow manufacturer guidelines for maintenance and replacement to ensure that the safety mechanisms remain effective.
Best Practices for Using Lifting Hooks
Ensuring safety during lifting operations requires adherence to several best practices. These practices not only protect personnel and equipment but also extend the lifespan of the lifting hooks.
Load Limit and Overloading
One of the cardinal rules in lifting operations is never to exceed the hook’s working load limit (WLL). Overloading can lead to permanent deformation or catastrophic failure of the hook. Always refer to the manufacturer’s specifications and ensure that both the hook and the connected rigging components (such as chains and slings) are rated for the intended load.
Proper Loading Techniques
Hooks must be loaded properly to distribute the load evenly. Improper loading, such as tip loading or side loading, can lead to bending or premature wear. Ensure that the load is centered and balanced. In addition, avoid exposing hooks to sharp objects or impacts that could compromise their structural integrity.
Matching Hook and Chain Capacities
When attaching hooks to chains or other rigging components, it is essential that the load-bearing capacities of each element are compatible. Mismatched capacities can create weak links in the system, which may result in failure under load. Verify that the hook’s specifications align with those of the chain, sling, or hoist used in the lifting operation.
Environmental Considerations
Lifting hooks are designed to operate within specific temperature ranges, typically from –40°F to 400°F. Exposure to corrosive substances or extreme temperatures can degrade the hook’s strength over time. Operators should be cautious when working in harsh environments and consider additional protective measures, such as coatings or regular maintenance schedules, to safeguard the equipment.
Special Considerations for Extreme Conditions
Extreme environmental conditions pose unique challenges to lifting operations. Understanding how these factors affect lifting hooks can prevent unforeseen accidents and equipment failure.
Cold Weather Operations
In colder climates, low temperatures can cause loads to freeze to the ground, increasing the risk of sudden, uncontrolled movements when the load is released. Additionally, extreme cold can cause metal components to become brittle, reducing their load-bearing capacity. In such conditions, it is advisable to use hooks that have been specifically rated for cold weather operations and to implement additional safety measures, such as pre-heating or using specialized lubricants.
High Temperature and Corrosive Environments
Conversely, high temperatures and corrosive substances can accelerate the wear and tear of lifting hooks. Heat can weaken the metal, while corrosive agents can lead to surface degradation. Regular inspections become even more critical in these environments. Use protective coatings where applicable and ensure that any signs of corrosion are addressed immediately to maintain the hook’s integrity.
Real-Life Examples and Data
Historical data from various industries indicate that improper handling of lifting hooks under extreme conditions has led to significant accidents and financial losses. By adopting best practices and leveraging specialized equipment designed for extreme conditions, many organizations have reported a reduction in incident rates by as much as 30%. These examples underscore the importance of understanding environmental impacts and adjusting operational protocols accordingly.
Choosing the Right Lifting Hook for Your Project
Selecting the right lifting hook involves a detailed assessment of the project’s requirements. Begin by evaluating the weight, shape, and balance of the load. The hook should be chosen not only for its load-bearing capacity but also for its compatibility with other rigging components.
Step-by-Step Guidelines:
Determine the Load Requirements:
Calculate the total weight and distribution of the load. Consider whether the load is static or dynamic, as this will influence the type of hook and additional safety features needed.
Assess the Environment:
Evaluate the operating environment. Is the job site exposed to extreme temperatures or corrosive substances? Choose a hook with appropriate material properties to withstand these conditions.
Match the Hook to the Rigging System:
Ensure that the lifting hook is compatible with the slings, chains, and hoists in your rigging system. Compatibility prevents overloading and minimizes wear on individual components.
Inspect and Maintain Regularly:
Establish a routine inspection schedule. Regular maintenance checks can identify early signs of damage or wear, allowing for timely replacements before safety is compromised.
Checklist for Selection:
Verify the hook's working load limit (WLL).
Confirm material compatibility with the environmental conditions.
Ensure proper match with other rigging components.
Consider additional safety features like integrated safety latches.
Regularly review manufacturer guidelines and industry standards.
Frequently Asked Questions (FAQs)
Q1: What should I do if I notice signs of wear on my lifting hook?
A1: Immediately remove the hook from service and inspect the entire rigging system for potential issues. Replace any components that show signs of deformation, corrosion, or fatigue.
Q2: How often should lifting hooks be inspected?
A2: Regular inspections should be performed before each lifting operation. A thorough, documented inspection should also occur on a scheduled basis—typically monthly or quarterly, depending on the workload and environmental conditions.
Q3: Can I use the same lifting hook for different types of loads?
A3: It is not recommended. Each lifting hook is designed for specific load types and configurations. Always select a hook that meets the precise requirements of your current operation to avoid overload and potential failure.
Q4: What role does temperature play in the performance of lifting hooks?
A4: Temperature extremes can affect metal properties. Cold weather can lead to brittleness, while high temperatures may weaken the metal. Always verify that the hook’s rated temperature range matches your operating conditions.
lifting hook safety is a multifaceted issue that requires careful attention to design, load requirements, environmental conditions, and regular maintenance. By understanding the differences between hook types—whether eye hooks, clevis hooks, swivel hooks, or others—and by adhering to best practices for usage, you can significantly reduce the risk of accidents and equipment failure during lifting operations.
At the core of every safe lifting operation is a commitment to rigorous inspection, proper training, and the use of components that meet industry standards. Whether you are managing a large construction site or a specialized manufacturing operation, selecting the right lifting hook and ensuring its optimal performance is critical for maintaining safety and operational efficiency.
If you have any questions or require expert advice on choosing the correct lifting hook for your project, do not hesitate to contact our specialized team. Our experts are ready to provide detailed guidance tailored to your specific needs, ensuring that your lifting operations remain safe and efficient at all times.
Article Navigation
PRECAST CONCRETE ACCESSORIES
OTHER RELATED ARTICLE
- 1.The importance of tension in lifting building accessories
- 2.How to Use Lifting Anchors for Precast Concrete
- 3.Lifting Clutch: Definition, Operation Guide and Comprehensive Analysis of Supplier Selection
- 4.Lifting Clutch VS Lifting Ring Clutch:Definition, Working Principle, Application Scenarios, and Selection Guide
Other Precast Concrete Accessories You Might Want to Know
You can click to learn more about HULK Metal precast concrete accessories such as lifting anchors, precast sockets, spread anchors, shuttering magnets, cast-in channels, wire loop boxes, and other precast concrete accessories you might want to know.
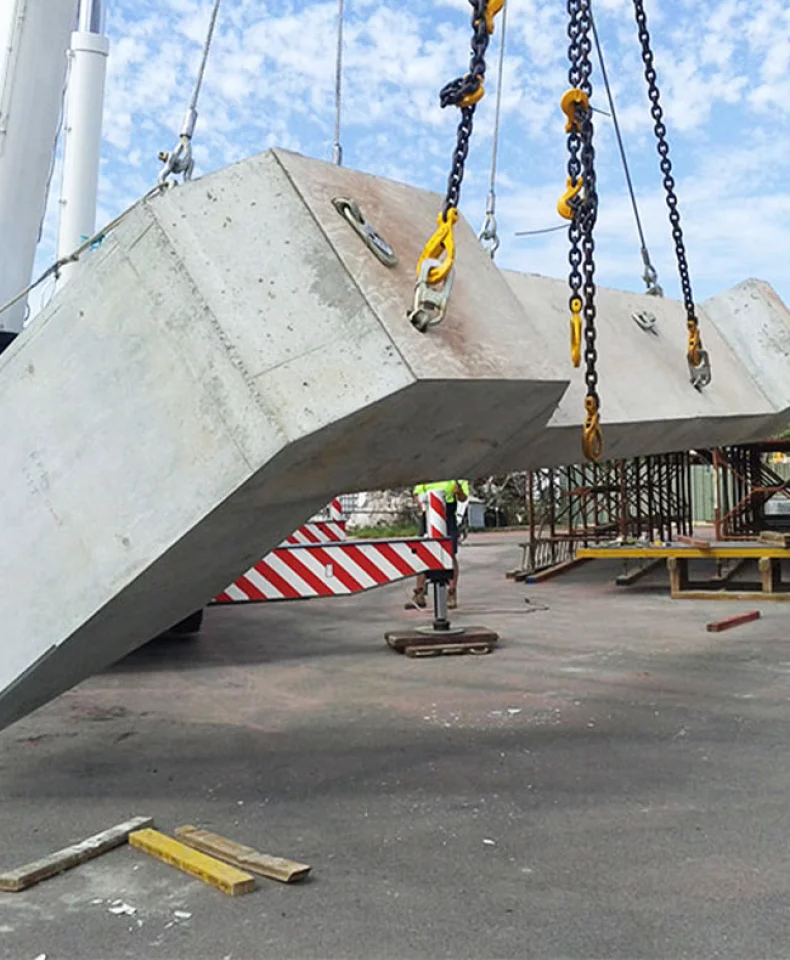