Advancements in Construction Efficiency: Precast Magnets for Electrical Conduit and Electric Box Fixing
Article Guidance:
I. Evolution of Construction Techniques
II. Understanding Precast Magnets
III. Advantages of Using Precast Magnets
IV. Considerations for Implementation
V. Case Studies: Success Stories in Construction
VI. Future Trends and Innovations
In the ever-evolving landscape of construction, the quest for efficiency and precision remains paramount. As construction methodologies continue to advance, so too do the tools and technologies that support them. One such innovation that has significantly contributed to streamlining construction processes is the utilization of precast magnets for electrical conduit and electric box fixing. These magnetic solutions have revolutionized the way electrical systems are installed, providing a reliable, time-saving, and cost-effective alternative to traditional methods.
I. Evolution of Construction Techniques
Traditional construction methods often involve intricate processes for fixing electrical conduits and electric boxes. Conventional techniques, such as drilling, anchoring, and welding, have been the go-to solutions for securing these essential components in place. However, as the demands for faster project completion and enhanced precision have increased, the construction industry has sought alternative methods to meet these challenges.
The evolution of construction techniques has seen a shift towards modular and precast construction. Prefabrication allows for the manufacturing of building components in controlled environments, reducing on-site labor and accelerating project timelines. Within this context, precast magnets have emerged as indispensable tools for securing electrical conduits and electric boxes with efficiency and accuracy.
II. Understanding Precast Magnets
Precast magnets are magnetic fixtures designed to securely hold and position prefabricated elements, such as electrical conduits and electric boxes, during the construction process. These magnets are engineered with powerful magnetic forces, ensuring a robust and reliable connection with ferrous surfaces. The application of these magnets eliminates the need for traditional fixing methods, providing a versatile and efficient solution for construction professionals.
A. Types of Precast Magnets
1. Electrical Conduit Fixing Magnets
Electrical conduit fixing magnets are specifically crafted to secure conduits in precast concrete elements. These magnets are designed to withstand the forces exerted during the concrete casting process, ensuring the conduits remain firmly in place. The magnets are strategically positioned on the formwork, holding the conduits securely until the concrete cures. This method significantly reduces installation time, labor costs, and potential errors associated with traditional fixing methods.
2. Electric Box Fixing Magnets
Similar to their conduit-fixing counterparts, electric box fixing magnets are tailored for the secure installation of electric boxes within precast concrete components. These magnets feature a design that accommodates the dimensions of electric boxes, holding them in place during the casting process. By utilizing magnetic forces, electric box fixing magnets offer a quick and precise solution, eliminating the complexities associated with traditional fixing methods.
III. Advantages of Using Precast Magnets
The adoption of precast magnets for electrical conduit and electric box fixing brings forth a multitude of advantages, contributing to the efficiency and success of construction projects.
A. Time Efficiency
One of the primary benefits of precast magnets is the substantial reduction in installation time. Traditional fixing methods often involve intricate steps, including drilling, anchoring, and welding, which can be time-consuming. Precast magnets streamline the process by securely holding conduits and electric boxes in place, allowing for faster assembly and, consequently, accelerated project timelines.
B. Cost-Effectiveness
By minimizing the labor-intensive tasks associated with traditional fixing methods, precast magnets contribute to significant cost savings. The efficient installation process translates to reduced labor hours, leading to lower overall project costs. Additionally, the reusability of precast magnets further enhances their cost-effectiveness, making them a valuable investment for construction projects of varying scales.
C. Precision and Consistency
Precast magnets ensure a high level of precision and consistency in the installation of electrical conduits and electric boxes. The magnets securely hold the components in their designated positions, eliminating the margin of error that may occur with traditional fixing methods. This precision is particularly crucial in construction projects where accurate placement of electrical systems is paramount for functionality and safety.
D. Versatility
The versatility of precast magnets is a key factor in their widespread adoption. These magnets are designed to accommodate various sizes and types of electrical conduits and electric boxes, providing a flexible solution for diverse construction needs. Whether the project involves residential, commercial, or industrial construction, precast magnets offer a versatile and adaptable solution for electrical system installations.
IV. Considerations for Implementation
While precast magnets offer numerous advantages, their effective implementation requires careful consideration of certain factors.
A. Magnetic Strength
The magnetic strength of precast magnets is a critical factor in their performance. The magnets must possess sufficient strength to securely hold electrical conduits and electric boxes in place during the casting process. Construction professionals should assess the specific requirements of their projects and select precast magnets with appropriate magnetic strength to ensure optimal results.
B. Compatibility with Formwork
The design and compatibility of precast magnets with the formwork used in construction are essential considerations. Magnets should seamlessly integrate with the formwork to facilitate easy installation and removal. Compatibility ensures a smooth construction process, minimizing disruptions and enhancing overall efficiency.
C. Reusability and Durability
The reusability and durability of precast magnets contribute to their long-term cost-effectiveness. High-quality magnets constructed from durable materials can withstand the rigors of construction environments, providing reliable performance over multiple projects. Evaluating the reusability and durability of precast magnets is crucial for making informed decisions regarding their integration into construction practices.
V. Case Studies: Success Stories in Construction
Numerous construction projects worldwide have successfully implemented precast magnets for electrical conduit and electric box fixing, showcasing the tangible benefits of this innovative technology.
A. Residential Construction
In a residential construction project focused on the rapid assembly of prefabricated elements, precast magnets played a pivotal role in expediting the installation of electrical conduits. The use of magnets resulted in a 30% reduction in installation time compared to traditional methods, leading to increased project efficiency and cost savings.
B. Commercial Development
In a large-scale commercial development, electric box fixing magnets were employed to streamline the installation of electrical boxes in precast concrete panels. The precision afforded by the magnets ensured consistent placement, contributing to the seamless integration of electrical systems. The project experienced a 20% reduction in labor costs and a 15% decrease in project completion time.
VI. Future Trends and Innovations
As the construction industry continues to evolve, ongoing research and development in the field of precast magnets are driving innovation and the emergence of new trends.
A. Smart Magnet Technology
The integration of smart technologies into precast magnets is an area of ongoing exploration. Smart magnet technology aims to enhance the monitoring and control of magnetic forces, allowing for real-time adjustments during the construction process. This innovation has the potential to further improve precision and adaptability, contributing to the continued optimization of construction practices.
B. Sustainable Materials
The use of sustainable materials in the manufacturing of precast magnets aligns with the growing emphasis on environmentally friendly construction practices. As the construction industry increasingly prioritizes sustainability, the development of magnets from recyclable and eco-friendly materials is poised to become a key trend in the evolution of precast magnet technology.
The integration of precast magnets for electrical conduit and electric box fixing represents a significant leap forward in construction efficiency. The advantages of time efficiency, cost-effectiveness, precision, and versatility position precast magnets as indispensable tools for modern construction projects. As the industry continues to embrace innovative solutions, the ongoing research and development in precast magnet technology promise to elevate construction practices to new heights of efficiency and sustainability.
Article Navigation
PRECAST CONCRETE ACCESSORIES
OTHER RELATED ARTICLE
Other Precast Concrete Accessories You Might Want to Know
You can click to learn more about HULK Metal precast concrete accessories such as lifting anchors, precast sockets, spread anchors, shuttering magnets, cast-in channels, wire loop boxes, and other precast concrete accessories you might want to know.
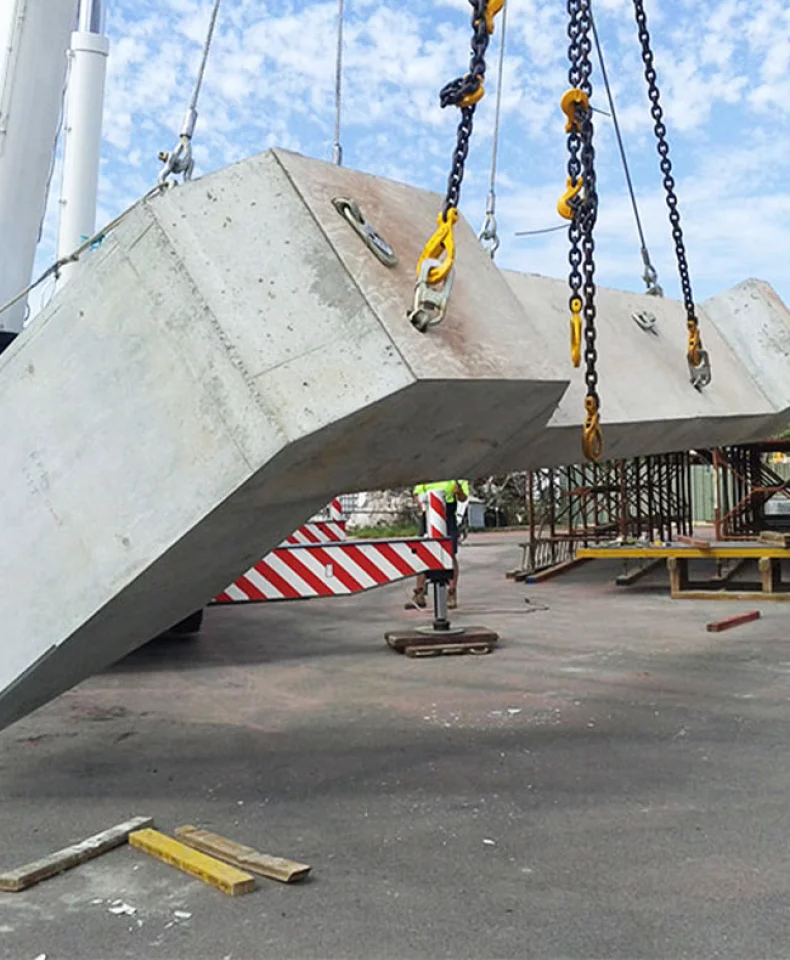