Key Factors in Choosing a Precast Concrete Lifting Clutch
Precast concrete elements are widely used in modern construction due to their efficiency, strength, and durability. However, ensuring the safe and effective lifting of these heavy components requires high-quality lifting clutches. A precast concrete lifting clutch is a crucial device that connects to embedded anchors, allowing for the secure and controlled lifting of concrete elements. Selecting the right lifting clutch is essential to guarantee safety, efficiency, and long-term performance in precast construction projects.
This article explores the key factors to consider when choosing a precast concrete lifting clutch, including material selection, safety factors, surface treatment, compatibility, load capacity, operational environment, and maintenance requirements. We will also highlight the advantages of choosing HULK Metal as your trusted supplier.
Overview of Precast Concrete Lifting Clutches
Definition and Function
A precast concrete lifting clutch is a specialized lifting device designed to securely attach to precast concrete anchors embedded within a structure. These clutches facilitate the safe and efficient movement of precast elements during manufacturing, transportation, and installation.
Common Types of Lifting Clutches
Precast concrete lifting clutches come in various designs, each suited for specific applications. The most common types include:
· Lifting Clutch – the lifting clutch is a specialized device used for securely attaching to embedded anchors in precast concrete elements, enabling safe lifting, transportation, and positioning in construction and industrial applications.
· Lifting Ring Clutch – the lifting ring clutch features a ring-shaped mechanism that securely locks onto lifting anchors in precast concrete, ensuring even load distribution, enhanced stability, and safe handling of heavy structural components.
Key Factors in Selecting a Lifting Clutch
Material Selection
The material of a lifting clutch directly affects its strength, durability, and resistance to wear. High-performance lifting clutches are typically made from:
· High-strength alloy steel – Such as 35CrMo, which offers excellent mechanical properties, including high tensile strength and toughness.
· Heat-treated carbon steel – Enhances durability and resistance to impact forces.
· Stainless steel – Suitable for environments requiring high corrosion resistance.
Choosing a lifting clutch made from high-quality materials ensures longevity and reduces the risk of failure during lifting operations.
Safety Factor
The safety factor is a critical consideration when selecting a lifting clutch. Industry standards recommend a minimum safety factor of 5:1, meaning the clutch should withstand five times the intended working load before failure.
· Higher safety factors ensure greater reliability and protect against unexpected loads or dynamic forces.
· Compliance with international safety standards, such as EN 13155 and ASME B30.20, guarantees superior performance and safety.
Surface Treatment
Surface treatment plays a crucial role in protecting lifting clutches from environmental factors, corrosion, and mechanical wear. Common surface treatments include:
· Galvanization – Provides corrosion resistance, especially in humid or marine environments.
· Powder coating – Enhances durability and improves the aesthetic appearance of the clutch.
· Electroplating – Increases resistance to rust and extends the service life of the clutch.
Choosing a lifting clutch with proper surface treatment ensures its long-term usability and minimizes maintenance requirements.
Compatibility with Embedded Anchors
A lifting clutch must be fully compatible with the embedded lifting anchors used in the precast elements. Key considerations include:
· Matching sizes and load ratings – The clutch must be designed to fit the corresponding anchor precisely.
· Ease of connection – A well-designed clutch should allow for quick and secure attachment to the lifting anchor.
· System compatibility – Ensure the clutch works seamlessly with the overall lifting system to prevent stress concentration and potential failures.
Load Capacity and Weight Distribution
Selecting a lifting clutch with an appropriate load capacity is essential to prevent overloading and potential failure. Factors to consider include:
· Weight of the precast concrete element – Choose a clutch rated for at least the maximum weight of the heaviest component.
· Load distribution – Ensure even weight distribution to reduce stress on the lifting system.
· Dynamic forces – Account for additional forces from wind, movement, and handling.
Operational Environment
The working environment significantly impacts the selection of a lifting clutch. Considerations include:
· Temperature range – Extreme temperatures can affect the performance of materials. Heat-treated alloys provide better resilience.
· Humidity and corrosion risks – Marine or chemical-rich environments require corrosion-resistant coatings.
· Outdoor vs. indoor use – Outdoor applications demand more robust surface protection to withstand weather conditions.
Maintenance Requirements
Proper maintenance extends the lifespan of a lifting clutch and ensures safe operation. Key maintenance considerations include:
· Regular inspections – Check for wear, cracks, or deformations before each use.
· Lubrication – Prevents rust and ensures smooth operation.
· Timely replacements – Replace worn or damaged clutches immediately to prevent accidents.
Following a structured maintenance plan enhances safety and prolongs the operational life of the lifting clutch.
Usage and Maintenance Guidelines
Proper Installation
Ensuring correct installation of the lifting clutch minimizes risks and improves operational efficiency. Key steps include:
· Check compatibility – Verify that the clutch matches the lifting anchor specifications.
· Secure attachment – Ensure the clutch is fully locked onto the anchor before applying load.
· Load testing – Perform a test lift to confirm stability and security.
Operational Precautions
· Avoid sudden movements – Prevent shock loading, which can cause stress fractures.
· Monitor weight limits – Never exceed the rated load capacity.
· Use trained personnel – Only qualified operators should handle lifting clutches.
Regular Inspection and Maintenance
· Inspect after every use – Check for deformation, cracks, or excessive wear.
· Keep records – Maintain logs of inspections and replacements.
· Store properly – Keep lifting clutches in dry, controlled environments to prevent corrosion.
Advantages of Choosing HULK Metal
Selecting the right lifting clutch supplier is just as important as choosing the clutch itself. HULK Metal offers industry-leading lifting solutions, backed by high-quality manufacturing and exceptional customer support.
Superior Product Quality
· Manufactured from high-strength alloy steel to ensure durability and reliability.
· Precision-engineered designs for secure and efficient lifting.
· Strict quality control to meet international safety standards.
Professional Technical Support
· Expert engineers provide customized lifting solutions tailored to project needs.
· Comprehensive installation guides and technical assistance.
· Responsive customer service to address any concerns or questions.
Customized Solutions
· OEM and custom design options available for specific project requirements.
· Flexible manufacturing capabilities to accommodate different lifting needs.
· Advanced testing and certification for guaranteed safety and performance.
Comprehensive After-Sales Service
· Hassle-free returns, exchanges, and replacements for defective products.
· Long-term partnership support, ensuring a reliable supply of high-quality lifting solutions.
· Global shipping and logistics support for efficient product delivery.
Choosing the right precast concrete lifting clutch is essential for ensuring safe and efficient lifting operations. Key factors such as material selection, safety ratings, surface treatment, compatibility, load capacity, and maintenance should be carefully evaluated before making a decision.
HULK Metal provides high-quality, reliable, and customized lifting clutches, backed by superior engineering and professional support. By choosing HULK Metal, you ensure enhanced safety, optimal performance, and long-term value for your precast construction projects.
Article Navigation
PRECAST CONCRETE ACCESSORIES
OTHER RELATED ARTICLE
- 1.The importance of tension in lifting building accessories
- 2.How to Use Lifting Anchors for Precast Concrete
- 3.Lifting Clutch: Definition, Operation Guide and Comprehensive Analysis of Supplier Selection
- 4.Lifting Clutch VS Lifting Ring Clutch:Definition, Working Principle, Application Scenarios, and Selection Guide
Other Precast Concrete Accessories You Might Want to Know
You can click to learn more about HULK Metal precast concrete accessories such as lifting anchors, precast sockets, spread anchors, shuttering magnets, cast-in channels, wire loop boxes, and other precast concrete accessories you might want to know.
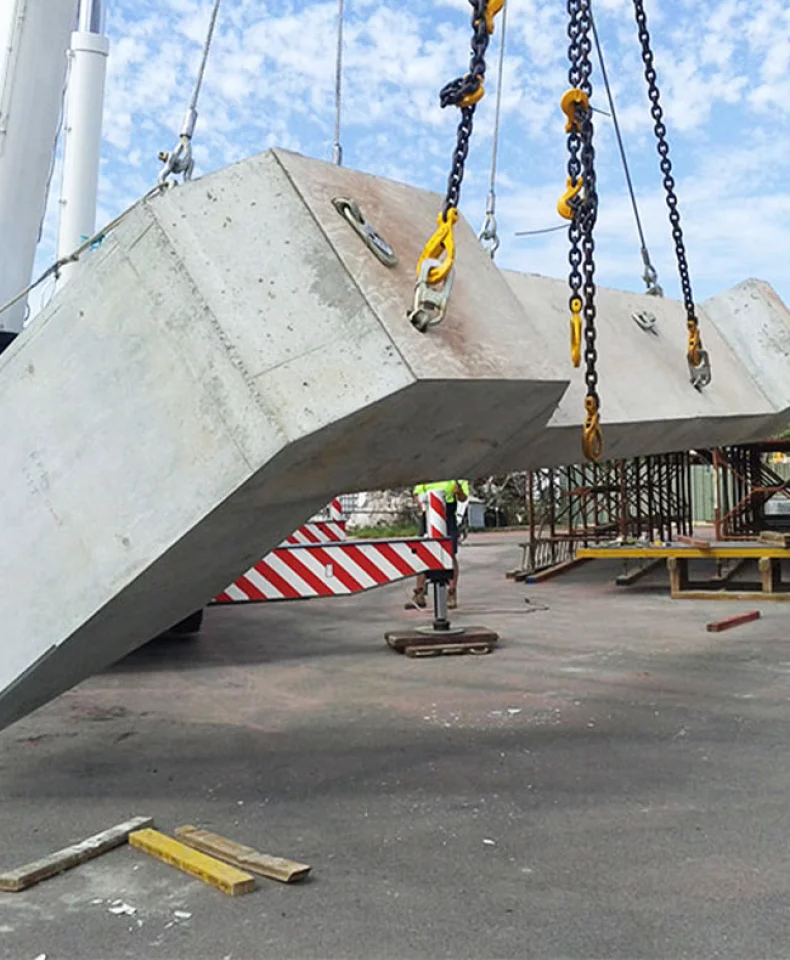